(A) The employer shall provide and require the use of personal
protective clothing and equipment, as specified in this rule, when employees
are required to work in a hazardous environment that may be encountered during
structural fire fighting activities and under similar conditions during
training activities.
(B) The employer shall assure that protective clothing protects
the head, body, and extremities and consists of at least the following
components: foot protection; hand protection; body protection; eye, face, and
head protection; and respiratory protection.
(C) Personal protective clothing and equipment shall be properly
sized for the wearer.
(D) Personal protective clothing and equipment that is damaged or
otherwise defective to the point of voiding its intended protection shall be
removed from service.
(E) Employers shall develop and require use of a written plan
covering the safe use, limitations, care, inspection, maintenance, and
replacement of the clothing and equipment required by this rule, and all
affected employees shall be trained in accordance with such plan.
(F) Employers shall develop and retain records for the life of
the protective clothing and equipment.
(G) Employer shall provide for the cleaning of personal
protective clothing.
(H) Where employees choose to provide their own protective
clothing and equipment, such clothing and equipment shall give equal or greater
protection than that provided by the employer.
(I) It shall be the responsibility of the employee to properly
use the equipment provided by the employer, as required in this
rule.
(J) Body protection.
(1) Body protection shall consist of a
protective coat and trousers, or equivalent protection.
(2) Protective clothing shall be
flame-resistant, durable, light-weight, water-resistant, nonirritating to the
skin, and cleanable as set forth in paragraph (J) of this rule.
(3) Protective clothing shall be cleaned
per the manufacturer's recommendations.
(4) Protective clothing for structural
fire fighting shall be repaired in accordance with manufacturer's
requirements.
If protective clothing cannot be repaired
properly without decreasing the protective qualities, it shall be
replaced.
(5) Protective clothing shall be designed
to give minimum interference to physical movement, the use of fire-fighting
tools, and protective breathing apparatus.
(6) There shall be at least a two inch
overlap of all layers of the protective coat and the protective trousers so
there is no gaping of the total thermal protection when the protective garments
are worn. The minimum overlap shall be determined by measuring the garments on
the wearer, without SCBA, in both of the following positions:
(a) "Position A": standing, hands together, reaching
overhead, as high as possible.
(b) "Position B": standing, hands together, reaching
overhead, with body bent forward, to the side, and to the back, as much as
possible.
(7) Employers that provide protective
coats with protective resilient wristlets secured through a thumb opening shall
be permitted to provide gloves of the gauntlet type for use with these
protective coats. Employers that do not provide such wristlets attached to the
protective coats shall provide gloves of the wristlet type for use with these
protective coats.
(8) Design requirements.
(a) Protective clothing shall consist of an outer shell, moisture
barrier, and thermal barrier.
(b) A means shall be provided to secure the moisture barrier and
thermal barrier to the outer shell.
(c) Garments, including the front closure, shall be constructed
in a manner that provides secure and complete moisture and thermal protection.
Closure systems shall be secured with positive locking fasteners including, but
not limited to, hooks and dees or zippers. Nonpositive fasteners, such as snaps
or hook and pile tape, shall not be used as positive locking fasteners but
shall be permitted to be utilized as supplementary garment closure
devices.
(d) Moisture barriers and thermal barriers shall extend to
within three inches (seventy-five mm) of the outer shell at the cuffs and hems
of protective garments. At the neck, the coat moisture barrier and thermal
barrier shall extend to the neckline seam. At the waist, the trouser moisture
barrier and thermal barrier shall extend to the waistline seam. In coats, the
moisture barriers and thermal barriers shall also extend to within one inch
(twenty-five mm) of the sleeve end of the outer shell, and in trousers shall
extend to within three inches (seventy-five mm) of the bottom outer shell hems.
The liner system shall be attached at or adjacent to the end of the coat
sleeves or the end of the trouser legs. Any mechanism used to attach the liner
system at or adjacent to the end of the coat sleeves and the end of the trouser
legs shall not be greater than one inch (twenty-five mm) between the attachment
points, and shall not be expandable. Moisture barriers and thermal barriers
shall be configured in a manner that provides continuous moisture and thermal
protection.
(e) Cargo pockets, where provided, shall have a means of drainage
of water and shall have flaps with a means of fastening them in the closed
position.
(f) Trim used to meet visibility requirements shall be no less
than two inches (fifty mm) wide and shall have retroreflective and fluorescent
areas. Retroreflective areas of trim shall be no less than five-eighths inch
(sixteen mm) wide. Fluorescent areas of trim shall have a minimum surface of
two inches2/linear inch (fifty
mm2/linear mm). Fluorescent and
retroreflective areas of trim shall appear to be continuous at a distance of
one hundred feet (30.5 m) for the length of the trim, with gaps between areas
of retroreflectivity of no more than one-eighth inch (3mm).
(g) Trim affixed to protective garments for the purpose of
meeting visibility requirements specified in paragraph (J)(12)(q) of this rule
may be obscured by garment components such as, but not limited to, pockets,
storm flaps, and reinforcing patches, as long as the minimum trim required in
paragraphs (J)(8)(f), (J)(9)(e), and (J)(10)(c) of this rule is not obscured.
(h) The outer shell and each separable layer of protective
garments shall have a label permanently and conspicuously attached to the
inside upon which at least the following warnings and information are is
printed:
(i) "This structural fire fighting garment meets the garment
requirements of NFPA 1971, 2013 Edition."
(ii) Manufacturer's name, identification, or
designation.
(iii) Manufacturer's address.
(iv) Country of manufacture.
(v) Manufacturer's element identification number, lot
number, or serial number.
(vi) Date of manufacture (not coded).
(vii) Model name, number, or design.
(viii) Size.
(ix) Principal material(s) of construction.
(x) Cleaning precautions.
(xi) Certification organization's label, symbol, or
identifying mark.
(i) The manufacturer shall provide a user information guide that
describes the care, use, inspection, maintenance, limitations, and replacement
of personal protective clothing.
(9) Additional requirements for
protective coats.
(a) Protective coats shall provide protection to the upper torso,
neck, arms, and wrists, excluding the hands and head.
(b) Protective coat hardware shall not penetrate through the
outer shell, moisture barrier, and thermal barrier to contact the wearer's
body when the coat is worn with closures fastened, unless the hardware is
completely covered by external closure flaps.
(c) Each protective coat sleeve shall have a permanent protective
wristlet, made of an inherently flame-resistant fiber, meeting requirements as
specified in paragraph (J)(12) of this rule. The wristlet shall be attached to
the protective coat sleeve in a manner that will not permit a gap in the
thermal protection.
(d) Protective coats shall have a composite collar no less than
three inches (seventy-five mm) in height at any point with a closure system.
The collar and closure system shall consist of an outer shell, moisture
barrier, and thermal barrier that meet all performance requirements as
specified in paragraph (J)(12) of this rule.
(e) Each protective coat shall have a drag rescue device (DRD)
installed in the upper torso portion of the coat. It shall be accessible from
the exterior of the garment. It shall be designed so that when deployed, the
DRD secures the fire fighter by the upper torso or shoulders so that the DRD
pulls directly on the body and shall not pull only the garment.
(f) The trim configuration for the coat shall be in accordance
with figure 1. The minimum trim pattern for the coat shall have one
circumferential band of trim or a staggered three hundred sixty-degree
visibility pattern meeting or exceeding the surface area of a continuous
circumferential band around the bottom of the coat. Where a staggered pattern
is used in the lower circumferential trim band, the lower edge of the upper
trim piece shall not be higher than the upper edge of the lower trim piece. The
lower edge of the circumferential band on the lower part of the coat shall be
within one inch (twenty-five mm) of the coat hem's highest point. The
front of the coat shall also have at least one band of horizontal trim at the
chest level. No vertical stripes of trim shall be permitted on the front of the
coat. The back of the coat shall also have a minimum of either two vertical
stripes of trim, perpendicular to the bottom band and with one strip located on
both the left and right sides of the of the back of the coat, or a minimum of
one horizontal band of trim at the chest/shoulder blade level. The minimum trim
configuration for each sleeve shall be one circumferential band, or a staggered
three hundred sixty-degree visibility pattern meeting or exceeding the surface
area of a continuous circumferential band, between the wrist and elbow level.
Where trim on the coat intersects a zipper, a maximum gap in the trim of one
inch (twenty-five mm) shall be permitted.
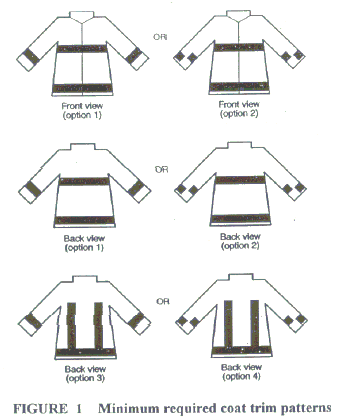
(10) Additional requirements for
protective trousers.
(a) Protective trousers shall provide protection to the lower
torso and legs, excluding the ankles and feet.
(b) Protective trouser hardware shall not penetrate through the
outer shell, moisture barrier, and thermal barrier to contact the wearer's
body when the trouser is worn with closures fastened, unless the hardware is
located on or above the waistline or the hardware is completely covered by
external closure flaps.
(c) The trim configuration for the trousers shall be in
accordance with figure 2. Protective trouser trim shall include a
circumferential band around each leg between the hem and knee. Where trim on
the trousers intersects a zipper, a maximum gap in the trim of one inch
(twenty-five mm) shall be permitted.
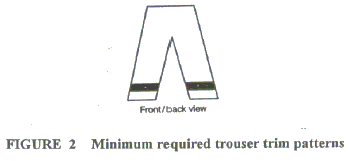
(11) Additional requirements for
protective coveralls.
(a) That portion of the protective coverall which corresponds to
the protective coat shall meet all requirements of paragraph (J)(9) of this
rule.
(b) That portion of the protective coverall which corresponds to
the protective trouser shall meet all requirements of paragraph (J)(10) of this
rule.
(12) Performance
requirements.
Protective garments shall be capable of
withstanding all tests specified in NFPA 1971, "Protective Ensemble for
Structural Fire Fighting, 2013 Edition."
(K) Foot protection.
(1) Design requirements.
(a) Protective footwear shall consist of a sole with heel, upper
with lining, an insole, a puncture-resistant device, a ladder shank or whole
sole equivalent and an impact and compression-resistant toecap permanently
attached.
(b) Protective footwear shall be no less than ten inches in
height when measured from the plane of the wear surface at the heel to the
lowest point of the throat.
(c) The heel breast shall be no less than one-half inch or more
than one inch. The heel breasting angle shall be no less than ninety degrees or
more than one hundred thirty-five degrees. The edges shall not be less than, or
extend more than, one-half inch laterally from the upper at any point. The
width of the footwear heel shall be equal to or greater than the width of the
sole at the intersection of the heel breast and the sole bottom.
(d) Metal parts shall not penetrate from the outside to the
lining or insole at any point. All hardware and external fittings shall be free
of rough spots, burrs, or sharp edges.
(e) No metal parts, including but not limited to nails or screws,
shall be present or used in the construction or attachment of the sole (with
heel) to the puncture-resistant plate, insole, or upper.
(f) The puncture-resistant device shall cover the maximum area of
the insole.
(2) Performance
requirements.
Protective footwear shall be capable of
withstanding all tests specified in NFPA 1971, "Protective Ensemble for
Structural Fire Fighting, 2013 Edition."
(3) Labeling requirements.
(a) Labels shall be legible to the naked eye and permanently
affixed to all protective footwear by stamping, embossing, gluing, or
stitching.
(b) Labels shall state:
(i) "This structural fire fighting protective footwear meets
the footwear requirements of NFPA 1971, 2013 Edition. Do Not Remove This
Label."
(ii) Manufacturer's name, identification, or
designation.
(iii) Manufacturer's address.
(iv) Country of manufacture.
(v) Size or size range.
(vi) Model or stock number.
(vii) Manufacturer's element identification number, lot or
serial number.
(viii) Month and year of manufacture.
(ix) Principle material(s) of construction.
(x) Cleaning precautions.
(xi) Certification organization's label, symbol, or
identifying mark.
(L) Head protection.
(1) Head protection shall consist of a
fire fighters' helmet and a protective hood. The helmet shall consist of a
shell, an energy-absorbing system, a retention system, retroreflective and
fluorescent markings, ear covers, and either a faceshield, or goggles, or
both.
(2) Each helmet shall be durably and
legibly labeled in a manner such that the label can be easily read without
removing any permanent helmet part. Each label shall include the following
information:
(a) "This structural fire fighting protective helmet meets
the helmet requirements of NFPA 1971, 2013 Edition. Do not remove this
label."
(b) Name, identification, or designation of
manufacturer.
(c) Manufacturer's address.
(d) Country of manufacture.
(e) Manufacturer's element identification number, lot
number, or serial number.
(f) Model number, name, or design.
(g) Month and year of manufacture (not coded).
(h) Cleaning precautions.
(i) Helmet size or size range.
(j) Principle material(s) of construction.
(k) Certification organization's label, symbol, or
identifying mark.
(3) The helmet manufacturer shall place a
unique manufacturer's part number, the symbol of the certification
organization, and the words "NFPA 1971, 2013 Edition" permanently on
each replaceable critical part of the goggle lens or faceshield.
(4) The helmet with faceshield/goggle
component(s) stowed shall provide peripheral vision clearance of at least
ninety-four degrees to each side when measured from the center of the eye with
the helmet positioned according to its helmet positioning index on the Alderson
fiftieth-percentile male headform.
(5) Where the goggle component is
selected, the goggles shall be permitted to be unattached, not assembled, to
the helmet
(6) When the faceshield or
faceshield/goggle component is deployed in accordance with its helmet
eye/face-positioning indexes on the Alderson fiftieth-percentile male headform,
the faceshield or faceshield/goggle component shall provide at least the
following field of vision when measured from the center of the
eye:
(a) A dihedral angle of at least eighty-five
degrees.
(b) An upper dihedral angle of at least ten degrees.
(c) A lower dihedral angle of at least forty
degrees.
(7) There shall be no openings
penetrating the shell except those provided by the manufacturer for mounting
energy-absorbing systems, retention systems, and accessories.
(8) The addition of helmet accessories
shall not interfere with the function of the helmet or its component parts and
shall not degrade the helmet's performance below the requirements of this
rule.
(9) The retention system shall include a
chin strap and a nape device. The chin strap shall have a minimum width of
three-fourths inch (nineteen mm).
(10) The helmet ear covers or portion of
the helmet providing the coverage of the ears, when deployed with the helmet
positioned on the ISO J headform according to its helmet positioning index,
shall provide at least the following coverage from the reference plane downward
to the lower edge of the ear covers:
(a) Three and three-fourths inches (ninety-five mm) where
measured two inches (fifty mm) forward of the coronal plane.
(b) Four and three-fourths inches (one hundred twenty mm) where
measured one inch (twenty-five mm) forward of the coronal plane.
(c) Five and one-eighth inches (one hundred thirty mm) where
measured at the coronal plane.
(d) Five and one-eighth inches where measured at the midsagittal
plane at the rear of the headform.
(11) All sewing thread used in the
construction of helmets shall be made of inherently flame-resistant
thread.
(12) Performance
requirements.
Helmets shall be capable of withstanding all
tests specified in NFPA 1971, "Protective Ensemble for Structural Fire
Fighting, 2013 Edition."
Label durability and legibility.
Labels shall remain in place and shall be
legible.
(M) Primary eye protection.
(1) Primary eye protection appropriate
for a given specific hazard shall be provided for and used by employees exposed
to that specific hazard.
(2) Primary eye protection shall meet the
requirements of ANSI Z87.1, 2010 edition, practice for occupational and
educational eye and face protection.
(3) The helmet faceshield, or flip-down
eye shields, alone shall not be considered and shall not be used as primary eye
protection.
(4) The full facepiece of SCBA, with the
regulator attached, shall constitute face and primary eye
protection.
(N) Protective hood
(1) The hood shall be designed to cover
and provide the limited protection to the head, face, and neck areas that do
not receive primary protection from the helmet or the "SCBA"
facepiece.
(2) The hood shall be donned properly, in
accordance with the manufacturer's instructions for wearing.
(3) The hood shall provide a minimum
coverage (as measured on the ISO size J headform) as follows:
(a) On each side measured downward from the reference plane at
the coronal plane of nine inches (two hundred thirty mm).
(b) In the back measured downward from the reference plane at the
rear midsagittal plane of thirteen inches (three hundred thirty
mm).
(c) In the front measured downward from the reference plane at
the front midsagittal plane, excluding the face opening, of twelve inches
(three hundred mm).
(4) The hood shall be designed with a
face opening. Other than where the hood face opening is designed to interface
with a specific "SCBA" facepiece or where the hood face opening is
designed to be adjustable, the opening shall measure five and five-eighths
inches, plus zero/minus one inch (one hundred forty-five mm, plus zero/minus
twenty-five mm) in any direction when the hood is laid out in a relaxed
condition on a flat surface, smoothed out, and with the face opening
up.
(5) Where the hood face opening is
provided with manual adjustment, the hood face opening shall be adjustable to
achieve a face opening of five and five-eighths inches (one hundred forty-five
mm).
(6) Where the hood face opening is
designed to interface with a specific "SCBA" facepiece, the hood face
opening shall overlap the outer edge of the specific "SCBA"
facepiece-to-face seal perimeter by not less than one-half inch (thirteen
mm).
(7) The hood shall have a label(s)
permanently and conspicuously attached upon which the following information is
legibly printed:
(a) "This structural fire fighting hood meets the hood
requirements of NFPA 1971, 2013 Edition. Do Not Remove this
label."
(b) Manufacturer's name, identification, or
designation.
(c) Manufacturer's address.
(d) Country of manufacture.
(e) Manufacturer's element identification number, lot
number, or serial number.
(f) Month and year of manufacture (not coded).
(g) Model name, number or design.
(h) Size or size range.
(i) Principle material(s) of construction.
(j) Cleaning precautions.
(k) Certification organization's label, symbol, or
identifying mark.
(8) Where the hood is designed to be used
with a specific "SCBA" facepiece(s), the hood manufacturer shall add
to the hood product label the following statement: "This hood is designed
to be used only with (Manufacturer to insert specific SCBA facepiece(s),
model(s), and size(s) in this space) for compliance with NFPA 1971. This hood
can only be used with the above noted facepiece(s)."
(9) Hoods shall be capable of
withstanding all tests specified in NFPA 1971, "Protective Ensemble for
Structural Fire Fighting, 2013 Edition."
Label durability and legibility.
Labels shall remain attached to the hood and
shall be legible to the unaided eye.
(O) Personal alert safety system ("PASS").
(1) Each member shall be provided with,
use, and activate his\her "PASS" device in all emergency situations
that could jeopardize that person's safety due to atmospheres that could
be IDLH, incidents that could result in entrapment, structural collapse of any
type, or as directed by the incident commander or incident safety
officer.
(2) Each "PASS" device shall be
tested at least weekly and prior to each use.
(3) Each "PASS" device shall be
maintained in accordance with the manufacturer's
instructions.
(4) Each "PASS" device shall
have a product label(s) permanently and conspicuously attached upon which the
following information is legibly printed:
(a) "This PASS meets the requirements of NFPA 1982, Standard
on Personal Alert Safety Systems (PASS), 2013 Edition. Do not remove this
label."
(b) Manufacturer name, identification, or
designation.
(c) Country of manufacture.
(d) Model name, number, or design.
(e) Identification, lot, or serial number.
(f) Month and year of manufacture (not coded).
(g) Recommended power source type and size if user
replaceable.
(h) Certification organization's label, symbol, or
identifying mark.
(i) "PASS" also shall meet the labeling requirements
for "Class I, Division I Hazardous Locations of ANSI/UL 913, 2013 Edition,
Standard for Intrinsically Safe Apparatus and Associated Apparatus for Use in
Class I, II, and III, Division I Hazardous Locations."
(5) "PASS" devices can be
designed to be either a stand-alone "PASS," or a
"SCBA-integrated PASS," which can be
removable/non-removable.
(6) PASS shall incorporate data logging
in nonvolatile memory and, at a minimum, the following events shall be
identified and recorded with the data log and shall also have a date and time
stamp for each event in the data log:
(a) When the PASS is turned on;
(b) When the PASS activates any alarm or pre-alarm;
(c) When the PASS alarm is activated by the user;
(d) When the PASS alarm was reset;
(e) When the PASS was turned off;
(f) When the PASS low power source warning signal
activates.
The data logging information shall be
downloadable by the employer.
(7) "PASS" shall incorporate a
mode selection device or devices to allow for operation in at least three
modes: "Off," "Alarm," and
"Sensing."
(a) All mode selection devices shall be capable of being
switched to the alarm or sensing mode by a single gloved hand.
(b) Only one action shall be required to switch the mode
selection device(s) from any mode to alarm.
(c) When "PASS" is sounding the alarm signal it shall
require at least two separate and distinct manual actions to silence the alarm
signal.
(8) PASS shall be provided with a light
source capable of providing a visual indication of mode status as well as an
audible source capable of providing an aural indication of a change in the mode
selection when switching from "off" to "sensing,"
"off" to "alarm," and "alarm" to
sensing."
(9) "PASS" shall incorporate a
motion detector, and while in the sensing mode, shall sound the alarm signal
when the "PASS" is motionless for thirty seconds, plus five/minus
zero seconds. The alarm signal shall be preceded by a pre-alarm signal that
shall sound ten seconds, plus three/minus zero seconds, before the sounding of
the alarm signal.
(a) The motion detector shall be operable regardless of the angle
of deployment of the "PASS."
(b) Any failure of the motion detector shall cause the
"PASS" to sound the alarm signal within thirty seconds, plus
five/minus zero seconds, of such failure.
(10) "PASS" shall emit an
audible operational signal within one second of being switched to sensing mode,
indicating to the user that the device is functioning properly.
(11) "PASS" shall have at least
an audible primary pre-alarm signal. The primary pre-alarm signal shall be a
distinct and different sound from the alarm signal. This signal shall sound no
more than ten seconds prior to the sounding of the alarm signal.
(12) "PASS" shall sound the
alarm signal when switched to the alarm mode. The alarm signal shall have a
duration of at least one hour at a sound pressure level of not less than
ninety-five dBa.
(13) While in the sensing mode,
"PASS" shall emit a recurrent audible low power source warning signal
when the battery voltage is depleted to the level that will maintain the alarm
signal level of at least ninety-five dBa for at least one hour. This sound
shall be distinct and different from the pre-alarm and alarm signals. The low
power source warning signal shall have an interval of not greater than thirty
seconds.
(14) The cancellation of the pre-alarm
signal or the silencing of the alarm signal shall automatically reset the
"PASS" to the sensing mode.
(15) "PASS" devices shall be
capable of withstanding all performance requirement tests specified in NFPA
1982, "Personal Alert Safety Systems (PASS), 2013
Edition."
Product label durability.
Product labels shall remain attached to the
"PASS" and shall be legible to the unaided eye.
(P) Respiratory protection.
(1) All fire fighters exposed to
hazardous atmospheres from fires and other emergencies, or where the potential
for such exposure exists, shall be provided with self-contained breathing
apparatus ("SCBA") approved by the national institute for
occupational safety and health (NIOSH) and the national fire protection
association (NFPA).
(2) The fire department shall adopt and
maintain a respiratory protection program that addresses the selection,
inspection, safe use, and maintenance of respiratory protection equipment,
training in its use, and the assurance of air quality testing.
(3) All members who might be required to
use respiratory protection equipment shall be medically certified by a
physician, or by a state of Ohio licensed health care professional who can
perform medical evaluations under the supervision of a physician, on an annual
basis. Medical certification can be obtained by a medical examination, or by
using the medical questionnaire as referenced in CFR 1910.134 Appendix
C.
(4) The facepiece seal capability of each
member qualified to use "SCBA" shall be verified by quantitative fit
testing on an annual basis and whenever new types of "SCBA" or
facepieces are issued. Each new member shall be tested before being permitted
to use SCBA in a hazardous atmosphere. Only members with a properly fitting
facepiece shall be permitted by the fire department to function in a hazardous
atmosphere with "SCBA."
(5) Only "SCBA" with an
approved service life of thirty minutes or more shall be considered
acceptable.
(6) The following "SCBAs" shall
be considered to meet the requirements of this rule:
(a) Open circuit "SCBA" of the positive-pressure type
that operate only in the pressure demand mode.
(b) Open circuit "SCBA" of the positive-pressure type,
equipped with an air flow control device for doffing and donning purposes only.
Such air flow control device shall not permit the continued use of the
"SCBA" in the demand mode after donning.
(c) Closed circuit "SCBA" with a rated service life of
more than two hours and a minimum protection factor of five thousand, as
determined by an acceptable quantitative fit test performed on each individual.
Such "SCBA" are acceptable only when long-duration respiratory
protection is deemed necessary by the employer. Closed circuit "SCBA"
shall operate in the positive-pressure mode only.
(7) Open circuit "SCBA"
approved by NIOSH for use in the demand mode or for use in both the demand mode
and the pressure demand mode are prohibited.
(8) Breathing air used to fill SCBA
cylinders shall meet the requirements specified in NFPA 1989, "Standard on
Breathing Air Quality for Emergency Services Respiratory
Protection."
(9) Breathing air quality shall be tested
quarterly by an accredited testing laboratory and shall meet the requirements
of paragraph (P)(8) of this rule. This shall also apply to vendor-supplied and
other fire department-supplied compressed breathing air. The department
receiving supplied air shall require the supplier to provide documentation that
the air received has been tested quarterly and that it meets the requirements
of paragraph (P)(8) of this rule. Written records shall be
maintained.
(10) The employer shall not permit any
known interference with the facepiece-to-face seal or with the operation of the
exhalation valve on the full facepiece of an "SCBA" on employees who
are exposed to hazardous atmospheres from fires and other emergencies or where
the potential for such exposure exists.
(11) Respiratory equipment shall be
inspected, maintained, and repaired in accordance with the manufacturer's
recommendations. Maintenance shall include at least:
(a) A written record of such inspection and maintenance for each
piece of equipment.
(b) Regulator calibration performed by a manufacturer-authorized
person at no more than twelve-month intervals.
(12) All compressed air cylinders used
with self-contained breathing apparatus shall meet department of transportation
(DOT) and NIOSH criteria.
(13) SCBA cylinders shall be
hydrostatically tested within the periods specified by the manufacturer and by
DOT and NIOSH.
(14) The practice of buddy breathing,
also known as an emergency escape breathing support system (EEBSS), may be
utilized where it is accomplished through the use of an NFPA and NIOSH-approved
connection that does not compromise the system integrity of either of the users
giving or receiving air.
(15) The use of a universal air connection
for rapid refilling of SCBA while being worn by the user shall only be done
under the following conditions:
(a) Manufacturer permitted, NIOSH-approved fill options are
used.
(b) An imminent life threatening situation occurs that requires
immediate action to prevent the loss of life or serious injury.
(c) Prior to a life threatening situation occuring that could
require immediate action to prevent the loss of life or serious
injury.
(d) The risk assesment process has identified procedures for
limiting personnel exposure during the refill process and has provided for
adequate equipment inspection and member safety.
(Q) Hand protection.
(1) Hand protection shall consist of
properly sized protective gloves or a glove system which allows dexterity of
hand movement and a sense of feel for objects.
(2) Gloves of the wristlet type or other
interface component shall be required if the protective coat does not provide a
protective resilient wristlet with a thumb opening.
Gloves of the gauntlet type shall be allowed if
the protective coat provided has a protective resilient wristlet with a thumb
opening.
(3) Gloves shall be maintained and
repaired in accordance with the manufacturer's requirements. If gloves
cannot be repaired properly without decreasing the protective qualities
required by this rule, they shall be replaced with gloves that meet the
requirements of paragraph (Q) of this rule.
(4) A label which includes the following
information shall be permanently attached to each glove:
(a) "This structural fire fighting glove meets the glove
requirements of NFPA 1971, Standard on Protective Ensemble for Structural Fire
Fighting, 2013 Edition. Do Not Remove This Label."
(b) Manufacturer's name, identification, or
designation.
(c) Manufacturer's address.
(d) Manufacturer's element, identification , lot or serial
number.
(e) Month and year of manufacture (not coded).
(f) Size or size range.
(g) Principle material(s) of construction.
(h) Cleaning precautions.
(i) Certification organization's label, symbol, or
identifying mark.
(5) Design requirements.
(a) Gloves for structural fire fighters shall be made of durable
outer material designed to withstand the effects of flame, heat, vapor,
liquids, sharp objects, and other hazards that are encountered during
structural fire fighting.
(b) Gloves shall be designed to give minimum interference to
physical movement, the use of fire fighting tools, and
"SCBA."
(c) Wrist protection shall be designed to prevent burns or injury
by providing complete covering under all conditions to the wrist
area.
(d) Wrist protection may be provided by either of the following
methods:
(i) Gloves, including wristlets, that extend no less than two
inches above the wrist crease as shown in figure 4 to this rule;
or
(ii) Wristlets attached to the sleeves of the protective coat that
extend to fit around the palm of the hand (see figure 4).

(e) Gloves shall be close-fitting above the wrist to restrict
entry of liquids, embers, and other foreign particles.
(f) The glove material in contact with the skin shall be
nonirritating.
(6) Performance
requirements.
Gloves shall be capable of withstanding all
tests specified in NFPA 1971, "Protective Ensemble For Structural Fire
Fighting, 2013 Edition."
Label durability and legibility.
Labels shall remain in place, and shall be
legible.
(R) Fall protection.
(1) Life safety rope.
(a) Technical-use life safety rope shall have a diameter of
three-eighths inch (9.5 mm) or greater and less than one-half inch(12.5 mm). It
shall have a minimum breaking strength of not less than four thousand four
hundred ninety-six lbf (twenty kn). The minimum elongation shall be less than
one per cent at ten per cent of breaking strength, and the maximum elongation
shall not be more than ten per cent at ten per cent of breaking
strength.
(b) General-use life safety rope shall have a diameter
seven-sixteenths inch ( eleven mm) or greater and not more than five-eighths
inch ( sixteen mm). It shall have a minimum breaking strength of not less than
eight thousand nine hundred ninety-two lbf (forty kn). The minimum elongation
shall not be less than one per cent at ten per cent of breaking strength, and
the maximum elongation shall not be more than ten per cent at ten per cent of
breaking strength.
(c) Life safety rope shall be constructed of virgin fiber and
shall be of block creel construction. Load-bearing elements shall be
constructed of continuous filament fiber.
(d) Fiber used for life safety rope shall have a melting point of
no less than four hundred degrees Fahrenheit.
(e) Each life safety rope shall have a product label. The label
shall be permitted to be a hang tag affixed to each individual life safety rope
or shall be permitted to be printed on a sheet that is inserted and sealed in
the packaging that contains the life safety rope. At least the following
information shall be legibly printed on the label:
(i) "This rope meets the life safety rope requirements of
NFPA 1983, Standard on Life Safety Rope and Equipment for Emergency Services,
2012 Edition."
(a) Class: manufacturer to insert specific information regarding
use rope.
(b) Minimum breaking strength: manufacturer to insert specific
information regarding pound/(Kn).
(c) Diameter: manufacturer to insert specific information
regarding inch/(mm).
(d) Type of fiber(s).
(ii) Manufacturer's name, identification, or
designation.
(iii) Manufacturer's address.
(iv) Country of manufacturer.
(v) Manufacturer's product identification.
(vi) Manufacturer's model, style, serial, or lot
number.
(vii) Certification organization's label, symbol, or
identifying mark.
(viii) Elongation at three hundred lbf (1.35 kN), at six hundred lbf
(2.7 kN), and at one thousand lbf (4.4 kN).
(f) In addition to the product label specified in paragraph
(R)(5)(e) of this rule, each life safety rope shall be marked for its full
length by insertion of a continuous identification tape. At least the following
statement and information shall be legibly printed on the tape not less than
once every thirty-nine inches (one meter):
(i) "Meets requirements for life safety rope of NFPA
1983."
(ii) Certification organization's label, symbol, or
identifying mark.
(iii) Name of manufacturer.
(iv) Year and quarter of manufacturer (not coded).
(g) The manufacturer of life safety rope shall furnish the
purchaser with at least use criteria, inspection procedures, maintenance
procedures, and retirement criteria.
(h) Life safety rope shall be inspected after being used for
rescue at fires or other emergency incidents or for training. It may be reused
if inspected before and after each such use in accordance with the
manufacturer's instructions and provided that:
(i) The rope has not been visually damaged by exposure to heat,
direct flame impingement, chemical exposure, or abrasion; and
(ii) The rope has not been subjected to any impact load;
and
(iii) The rope has not been exposed to chemical liquids, solids,
gases, mists, or vapors of any material known to deteriorate rope;
and
(iv) The rope passes inspection when inspected by a qualified
person following the manufacturer's inspection procedures.
(2) Life safety harness.
(a) Life safety harnesses shall be designed and designated in
accordance with one of the following classes:
(i) Harness that fastens around the waist and around thighs
or under buttocks and designed for rescue with a design load of six hundred lbf
shall be designated as class II life safety harness.
(ii) Harness that fastens around waist, around thighs or
under buttocks, and over shoulders, designed for rescue with a design load of
six hundred lbf shall be designated as class III life safety harness. Class III
life safety harness shall be permitted to consist of one or more
parts.
(b) Life safety harness shall be permitted to be adjustable
within a range of sizes, provided in a range of sizes, or custom-fitted for
individuals.
(c) Load-bearing textile materials used to construct life safety
harness shall be constructed of virgin, synthetic, continuous filament
fiber.
(d) All webbing ends shall be secured by heat-sealing or by
another method that prevents unraveling.
(e) All thread shall be compatible with webbing used, shall meet
the strength and heat resistance requirements specified in paragraph (R)(2)(k)
of this rule, and shall allow for ease of inspection. All stitching breaks or
ends shall be backtacked no less than one one-half inch (thirteen
mm).
(f) Life safety harness shall have at least one load bearing
attachment point located at the front waist or sternal location of the
harness.
(g) Castings shall meet class I, grade A requirements of SAE-STD
2175A, "castings, classification and inspection of."
(h) Where a buckle is an integral part of a life safety harness,
the buckle manufacturer shall provide written evidence that all load-bearing
buckles have been proof-loaded to at least two thousand four hundred
seventy-three lbf (eleven kN).
(i) Each life safety harness shall have permanently affixed a
product label embossed, printed, sewn, stapled, riveted, or otherwise
permanently attached with a metal label plate. At least the following
compliance statement shall be on the product label:
(i) "This life safety harness meets the harness requirements
of NFPA 1983, "Life Safety Rope and Equipment for Emergency Services, 2012
edition"; class: (manufacturer to insert specific information regarding
class)."
The class designation shall be as
determined by the certification organization.
(ii) Name, identification, or designation of
manufacturer.
(iii) Manufacturer's address.
(iv) Country of manufacture.
(v) Manufacturer's product identification.
(vi) Manufacturer's lot, model, style, or serial
number.
(vii) Certification organization's label, symbol, or
identifying mark.
(j) In addition, for harnesses, at least the following
information shall be provided on the label:
(i) For class II harnesses: "Fits waist size (manufacturer
to insert specific size(s)."
(ii) For one-piece class III harnesses: "Fits waist size
(manufacturer to insert specific size(s); fits height (manufacturer to insert
specific height(s)."
(iii) For multiple-piece class III harnesses: "Fits waist size
(manufacturer to insert specific size(s); fits height or chest size
(manufacturer to insert specific height(s) or chest size(s); fits height
(manufacturer to insert specific height(s). This is one part of a
multiple-piece harness and must be used in conjunction with component part
number (manufacturer to insert specific component part number[s]) in order to
fully meet the criteria of class III harness.
(k) Life safety harness shall be capable of withstanding all
tests specified in NFPA 1983, " Life Safety Rope and Equipment for
Emergency Services, 2012 Edition," with the following
results:
(i) Static test - upright (for class II and III).
(ii) Static test - horizontal (for class II and III).
(iii) Static test - head down (for class III).
Class II and III life safety harness shall
not release from the test torso, the harness buckles and adjusting devices
shall not slip more than one inch (twenty-five mm), and the harness shall show
no visible signs of damage that would affect its function.
(iv) For class III life safety harness that includes shoulder
attachment points, such shoulder attachment points shall be tested only during
the static test - upright. The shoulder attachment points shall not release
from the test torso, and shall show no signs of damage that would affect their
function.
(v) Fiber and thread used in the construction of life safety
harness shall have a melting point of no less than four hundred degrees
Fahrenheit.
(vi) Where class II and III life safety harness include side
"D-rings" and attachment points designated by the manufacturer as
positioning attachments only, these attachments shall show no visible signs of
damage that affect its function.
(vii) All metal hardware and parts shall show no more than light
surface-type corrosion or oxidation, and remain functional.
(l) The manufacturer of life safety harness shall furnish the
purchaser with at least use criteria, inspection procedures, maintenance
procedures, and retirement criteria for the product.
(3) Belt system.
(a) Belts shall be designed and designated in accordance with one
of the following types:
(i) A belt that fastens only around the waist and is intended
for use as a positioning device for a person on a ladder shall be designated as
a ladder belt.
(ii) A belt that fastens only around the waist and is intended for
use as a positioning device for a person on a ladder and also intended for use
only by the wearer as an emergency self-rescue device shall be designated as a
ladder/escape belt.
(b) All belts shall be permitted to be adjustable within a range
of sizes, provided in a range of sizes, or custom-fitted for
individuals.
(c) Load-bearing textile materials used in the construction of
all belts shall be made of virgin, synthetic, continuous filament
fiber.
(d) All belts shall have webbing ends secured by heat sealing or
by another method that prevents unraveling.
(e) All thread utilized in the construction of all belts shall be
compatible with the webbing used and shall allow for ease of inspection. All
stitching breaks or ends shall be backtacked not less than one-half (thirteen
mm).
(f) The ladder belt tether or device that connects the wearer to
a ladder shall be permanently affixed to the ladder belt and shall not be
greater than twenty-four inches (six-hundred ten mm) in length. This
requirement applies only to ladder belts as defined in paragraph (R)(3)(a)(i)
of this rule.
(g) Each belt shall have permanently affixed a product label
embossed, printed, sewn, stapled, riveted, or otherwise permanently attached
with a metal plate. At least the following compliance statement shall be on the
product label:
(i) "This belt meets the belt requirement of NFPA 1983,
"Life Safety Rope and Equipment for Emergency Services, 2012
Edition"; type (manufacturer to insert specific type)."
The belt type designation shall be
determined by the certification organization.
(ii) "Fits waist size (manufacturer to insert specific waist
size(s)."
(iii) Name, identification, or designation of
manufacturer.
(iv) Manufacturer's address.
(v) Country of manufacture.
(vi) Manufacturer's product identification.
(vii) Manufacturer's lot, model, style, or serial
number.
(viii) Certification organization's label, symbol, or
identifying mark.
(h) All ladder belts and ladder/escape belts shall be capable of
withstanding all tests specified in NFPA 1983, " "Life Safety Rope
and Equipment for Emergency Services, 2012 Edition."
(i) The manufacturer of belts shall furnish the purchaser with at
least use criteria, inspection procedures, maintenance procedures, and
retirement criteria for the product.
(4) Auxiliary equipment.
(a) Auxiliary equipment shall be designated by the manufacturer
for its intended use and design load as either escape, light-use, or
general-use.
(i) Escape shall apply to equipment intended for the sole use of
the rescuer for personal escape or self-rescue.
(ii) Technical-use shall apply to equipment intended for a design
load of three hundred lbf (1.33 kN).
(iii) General-use shall apply to equipment intended for design
loads of six hundred lbf (2.67 kN).
(b) Load-bearing hardware shall be constructed of forged,
machined, stamped, extruded, or cast metal. Castings shall meet Class I, Grade
A requirements of SAE-STD 2175A, "Castings, Classification and Inspection
of."
(c) Rope grab devices shall be designated for either technical
use or for general use.
(d) All load-bearing buckles shall have been proof loaded to at
least two thousand four hundred seventy-three lbf (eleven kn).
(e) Snap-link and carabiner gates shall be self-closing and of a
locking design.
(f) Webbing used to construct auxiliary equipment software shall
be constructed of virgin, synthetic, continuous filament fiber.
(g) All webbing ends shall be secured by heat sealing or by
another method that prevents unraveling.
(h) All thread used to construct auxiliary equipment software
shall be compatible with webbing used and shall allow ease of inspection. All
stitching breaks or ends shall be backtacked not less than one-half inch
(thirteen mm).
(i) Each item of auxiliary equipment shall be permitted to have a
hang tag affixed to each individual auxiliary equipment item or shall be
permitted to be printed on a sheet that is inserted and sealed in the packaging
that contains the item. At least the following compliance statements shall be
on the product label:
(i) "This (insert name of equipment item here) meets the
auxiliary equipment requirements of NFPA 1983, Life Safety Rope and Equipment
for Emergency Services, 2012 Edition."
(ii) Name, identification, or designation of
manufacturer.
(iii) Manufacturer's address.
(iv) Country of manufacture.
(v) Manufacturer's product identification.
(vi) Manufacturer's lot, model, style, or serial
number.
(vii) Certification organization's label, symbol, or
identifying mark.
(viii) Auxiliary equipment shall also be stamped, engraved, or
otherwise permanently marked with a "G" for general-use;
"T" for technical-use; "E" for escape, as designated in
paragraphs (R)(4)(a)(i) to (R)(4)(a)(iii) of this rule.
(ix) Portable anchor devices shall add to the product label:
"Minimum breaking strength and rating are determined at the configuration
of lowest strength per manufacturer's instructions."
(x) Rigging and anchor straps shall add to the product label:
"Minimum breaking strength and rating are determined using a basket (U)
configuration. In addition, this strap has a minimum breaking strength of:
[enter number here] kN in a choker configuration; [enter number here] kN when
pulled end to end."
(xi) Where detachable components must be used with the auxiliary
equipment in order for the auxiliary equipment to be compliant, shall add to
the product label: "To be compliant with NFPA 1983, the following
additional components must be used in conjunction with this (insert type of
auxiliary equipment here)."
(j) All auxiliary equipment shall be capable of withstanding all
tests specified in NFPA 1983, " "Life Safety Rope and Equipment for
Emergency Services, 2012 Edition."
(k) The manufacturer of auxiliary equipment shall furnish the
purchaser with at least use criteria, inspection procedures, maintenance
procedures, and retirement criteria for the product.
(5) Escape rope.
(a) Escape rope shall be constructed of virgin fiber and shall be
of block creel construction. Load-bearing elements shall be constructed of
continuous filament fiber.
(b) Escape rope shall have a diameter of 0.295 inch (19/64th
inch) (7.5 mm) or greater and less than three-eighths inch (9.5
mm).
(c) Escape rope shall have a minimum breaking strength of not
less than three thousand thirty-four lbf (13.5 kN).
(d) Elongation of all new escape rope shall be less than one per
cent and not more than ten per cent at ten per cent of breaking
strength.
(e) Fiber utilized for all escape rope shall not have a melting
point of less than four hundred degrees Fahrenheit (two hundred four degrees
Celsius).
(f) Each escape rope shall have a product label. The product
label shall be permitted to be a hang tag affixed to each individual escape
rope or shall be permitted to be printed on a sheet that is inserted and sealed
in the packaging that contains the rope. At least the following information
shall be legibly printed on the label:
(i) "This rope meets the escape rope requirements of NFPA
1983, Life Safety Rope and Equipment for Emergency Services, 2012
Edition."
(a) Minimum breaking strength: (manufacturer will insert specific
information regarding lbf/(kn).
(b) Diameter: (manufacturer will insert specific information
regarding inch/(mm).
(c) Type of fiber(s).
(ii) Manufacturer's name, identification, or
designation.
(iii) Manufacturer's address.
(iv) Country of manufacture.
(v) Manufacturer's product identification.
(vi) Manufacturer's product identification.
(vii) Certification organization's label, symbol, or
identifying mark.
(viii) Elongation at three hundred lb (1.35 kN), at six hundred lb
(2.7 kN), and at one thousand lb (4.4 kN).
(g) In addition to the product label specified in paragraph
(R)(5)(f) of this rule, each escape rope shall be marked for its full length by
insertion of a continuous identification tape. At least the following statement
and information shall be legibly printed on the tape not less than once every
thirty-nine inches (one meter):
(i) "Meets requirements for escape rope of NFPA
1983."
(ii) Certification organization's label, symbol, or
identifying mark.
(iii) Name of manufacturer.
(iv) Year and quarter of manufacturer (not coded).
(h) The manufacturer of escape rope shall furnish the purchaser
with at least use criteria, inspection procedures, maintenance procedures, and
retirement criteria.
(6) Throwline.
(a) Throwline shall be constructed of virgin fiber and shall be
of block creel construction. Load-bearing elements shall be constructed of
continuous filament fiber.
(b) Throwline shall have a diameter of 19/64th inch (seven mm) or
greater, but less than 3/8th inch (9.5 mm).
(c) The minimum breaking strength for new throwline shall not be
less than two thousand nine hundred twenty-three lbf (thirteen
kn).
(d) New throwline shall be tested for the ability to float and
shall float.
(e) Each throwline shall have a product label. The throwline
product label shall be permitted to be a hang tag affixed to each individual
throwline or shall be permitted to be printed on a sheet that is inserted and
sealed in the packaging that contains the throwline. At least the following
information shall be legibly printed on the label:
(i) "This rope meets the throwline requirements of NFPA
1983, Life Safety Rope and Equipment for Emergency Services, 2012
Edition."
(a) Minimum breaking strength: (manufacturer to insert specific
information regarding lbf/(kn).
(b) Diameter: (manufacturer to insert specific information
regarding inch/(mm).
(c) Type of fiber(s),
(ii) Manufacturer's name, identification, or
designation.
(iii) Manufacturer's address.
(iv) Country of manufacture.
(v) Manufacturer's product identification.
(vi) Manufacturer's model, style, serial, or lot
number.
(vii) Certification organization's label, symbol, or
identifying mark.
(f) In addition to the product label specified in paragraph
(R)(6)(e) of this rule, each throwline shall be marked for its full length by
insertion of a continuous identification tape. At least the following statement
and information shall be legibly printed on the tape not less than once every
thirty-nine inches (one meter):
(i) "Meets requirements for throwline of NFPA
1983."
(ii) Certification organization's label, symbol, or
identifying mark;
(iii) Name of manufacturer;
(iv) Year and quarter of manufacture.