(A) Final leveling of a manufactured home.
The manufactured home shall be leveled before completion of the installation. A home shall be considered level when no more than a quarter-inch difference exists between any two adjacent piers and no more than one-half inch difference exists between any point on the frame of the home to any comparable point on the frame on the opposite side or end of the home. Where two sections are joined at the marriage line, the maximum tolerance at the floor between the sections shall not exceed one-quarter inch vertical difference in height.
(B) Exterior close-up.
(1) Exterior siding and roofing necessary to join all sections of the home shall be installed according to the product manufacturer's installation instructions and shall be fastened in accordance with the designs and manufacturer's instructions and consistent with this rule. Exterior close-up strips/trim shall be fastened securely and sealed with exterior sealant (see figure 8A of this rule).
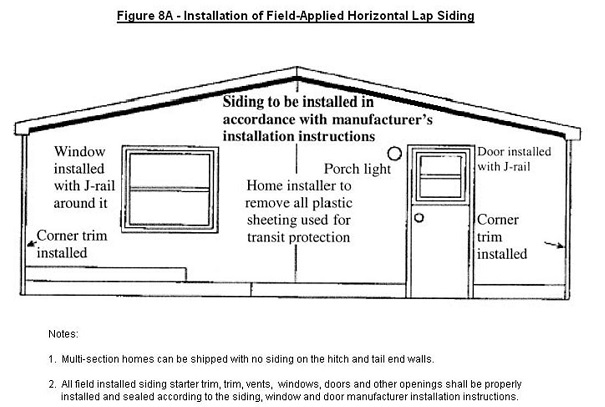
(2) Joints and seams. All joints and seams in exterior wall coverings that were disturbed during location of the home shall be made weatherproof.
(3) Prior to installing the siding, the polyethylene sheeting covering exterior walls for transit shall be completely removed.
(4) Holes in the roof made in transit or setup shall be made weatherproof and sealed with a sealant or other material that is suitable for use with the roofing materials in which the hole is made.
(5) Mate-line gasket. The installer shall use the home manufacturer's materials and designs for mate-line gaskets or other methods designed to resist the entry of air, water, water vapor, insects, and rodents at all mate-line locations exposed to the exterior when available. Where the mate-line gasket material is not available from the manufactured home manufacturer, two-inch foam sealed inside a vapor barrier sheathing type gasket, or one-inch by four-inch fiberglass roll, a batt, or its equivalent shall be installed in accordance with Figure 8B of this rule.
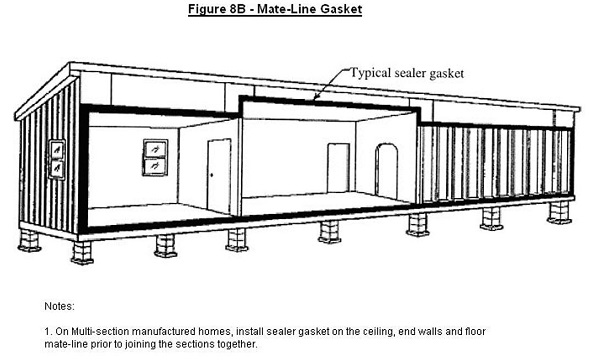
(6) Hinged roofs and eaves. Hinged roofs and eaves shall be completed during installation so as to comply with the MHCSS and these standards. However, some hinged roofs may be subject to specific on-site or alternative construction requirements issued separately by HUD. Generally, hinged roof homes are not subject to such special requirements as long as:
(a) The homes are designed to be located in wind zone one;
(b) The completed hinged roof pitch is less than seven units vertical in twelve units horizontal; and
(c) Fuel burning appliance flue penetrations are not above the hinge.
(C) Structural interconnection of multi-section homes.
(1) For multi-section homes, structural interconnections along the interior and exterior at the mate-line are necessary to join all sections of the home.
(2) The interconnections shall be completed in accordance with the manufactured home installation manual or, if not available, these standards to ensure a completely integrated structure.
(3) Upon completion of the exterior close-up, no gaps shall be permitted between the structural elements being interconnected along the mate-line of multi-section homes. However, prior to completion of the exterior close-up, minor gaps that do not exceed one inch shall be permitted between structural elements provided the gaps are closed before completion of close-up, the home sections are in contact with each other, and the mating gasket is providing a proper seal. Gaps greater than one-fourth inch shall be shimmed tight, and fastener lengths used to make connections between the structural elements shall be increased to provide adequate penetration into the receiving member. Gaps between one inch and one-fourth inch in the walls or floor shall be filled with plywood shims or its equivalent.
(4) Multi-section homes with no manufacturer's installation instructions shall be assembled by lagging the floor rim joist approximately center between the floor joists not to exceed twenty-four inches on centers. The lag bolt shall be a minimum three-eighths inch by five inches lag bolt or screw with a standard three eighths inch flat washer.
(5) Multi-section homes with no manufacturer's installation instructions shall be connected at the roof with one and one-half inch wide perforated strapping connecting one rafter to the opposite rafter, affixed with three-inch screws, two inches on each side of the ridge. Strapping shall be concealed by the ridge cap. Lags shall not be substituted for the strapping and screws unless the dimensional lumber to be joined by the lags is of sufficient size to accept the lags or required by an Ohio registered professional engineer or registered architect.
(6) Multi-section homes with no manufacturer's installation instructions shall be connected at the end walls with a number ten screw, four and one-half inches or approved equal, toe screwed every sixteen inches alternate sides.
(D) Bottom board repair.
(1) The bottom board covering shall be inspected for any loosening or areas that might have been damaged or torn during installation or transportation. Any missing insulation shall be replaced prior to closure and repair of the bottom board.
(2) Any splits or tears in the bottom board shall be resealed with bottom board fabric tape or patches in accordance with methods provided in the manufacturer's installation instructions. Duct tape shall not be used to repair bottom board.
(3) Plumbing P-traps shall be checked to be sure they are well insulated and covered.
(4) All edges of repaired bottom board areas shall be taped with bottom board fabric tape or otherwise equivalently sealed.
(E) Interior close-up.
(1) All shipping, blocking, strapping, or bracing shall be removed from appliances, windows, and doors.
(2) At a minimum, shipped-loose wall paneling necessary for the joining of all sections of the home shall be installed by using polyvinyl acetate (PVA) or equal adhesive on all framing members and fastened with minimum one-inch long staples or nails at six inches on center panel edges and twelve inches on center in the field, unless alternative fastening methods are required in the manufactured home's installation instructions. (See figure 8C of this rule).
(F) Stairway walking surface.
The walking surface of the treads and landings of stairways shall be sloped no steeper than one unit vertical in forty-eight units horizontal (two per cent slope).
(G) Handrails.
Handrails shall be provided on at least one side of each continuous run of treads or flights with four or more risers.
(1) Handrail height, measured vertically from the sloped plane adjoining the tread nosing, or finish surface of ramp slope, shall not be less than thirty-four inches (864 mm) and not more than thirty-eight inches (965 mm).
(2) Handrails for stairways shall be continuous for the full length of the flight, from a point directly above the lowest riser of the flight. Handrail ends shall be returned or shall terminate in newel posts or safety terminals. Handrails adjacent to a wall shall have a space of not less than one and one-half inch (38 mm) between the wall and the handrails.
(3) Exceptions:
(a) Handrails shall be permitted to be interrupted by a newel post at the turn.
(b) The use of a volute, turnout, start easing, or starting newel shall be allowed over the lowest tread.
(c) Two or more separate rails shall be considered continuous if the termination of the rails occurs over a single tread and within four inches (101.6 mm) of each other. If the transition occurs between a wall mounted handrail and handrail/guardrail combination, the wall mounted handrail shall return into the wall.
(H) Handrail grip size.
All required handrails shall be of one of the following types or shall be equivalent graspability.
(1) Type I. Handrails with a circular cross section shall have an outside diameter of at least one and one-fourth inches (32 mm) and not greater than two inches (51 mm). If the handrail is not circular, it shall have a perimeter dimension of at least four inches (102 mm) and not greater than six and one-fourth inches (160 mm) with a maximum cross section dimension of two and one-fourth inches (57 mm).
(2) Type II. Handrails with a perimeter greater than six and one-half inches (160 mm) shall provide a graspable finger recess area on both sides of the profile. The finger recess shall begin within a distance of three-quarters inch (19 mm) measured vertically from the tallest portion of the profile and achieve a depth of at least five-sixteenths inch (8 mm) within seven-eighths inch (10 mm) to a level that is not less than one and three-quarters inches (45 mm) below the tallest portion of the profile. The minimum width of the handrails above the recess shall be one and one-fourth inches (32 mm) to a maximum of 2 and three-quarters inches (70mm). Edges shall have a minimum radius of 0.01 inches (0.25 mm).
(I) Bulkhead enclosure stairways.
Stairways serving bulkhead enclosures, not part of the required building egress, providing access from the outside grade level to the basement shall be exempt from the requirements of this rule where the maximum height from the basement finished floor level to grade adjacent to the stairway does not exceed eight feet (2438 mm), and the grade level opening the stairway is covered by a bulkhead enclosure with hinged doors or other approved means. Where a stairway of two or fewer risers is located on the exterior side of a door, other than the required exit door, a landing is not required for the exterior side of the door.
(J) Ramps.
(1) Maximum slope. Ramps shall have a maximum slope of one unit vertical in eight units horizontal (12.5 per cent slope).
(2) Landings required. A minimum three-feet-by-three-feet (914 mm by 914 mm) landing shall be provided:
(a) At the top and bottom of ramps;
(b) Where doors open onto ramps; and
(c) Where ramps change direction.
(3) Handrails required. Handrails shall be provided on at least one side of all ramps exceeding a slope of one unit vertical in twelve units horizontal (8.33 per cent slope).
(4) Height. Handrail height, measured above the finished surface of the ramp slope, shall be not less than thirty-four inches (864 mm) and not more than thirty-eight inches (965 mm).
(5) Handrail grip size. Handrails on ramps shall comply with this rule.
(6) Continuity. Handrails where required on ramps shall be continuous for the full length of the ramp. Handrail ends shall be returned or shall terminate in newel posts or safety terminals. Handrails adjacent to a wall shall have a space of not less than one and one-half inches (38 mm) between the wall and the handrails.
(K) Landings at doors.
(1) There shall be a floor or landing on each side of each exterior door, except as follows:
(a) The floor or landing at the interior side of the exit door required by rule 4781-6-03.9 of the Administrative Code shall not be more than one and one-half inches (38 mm) lower than the top of the threshold. The floor or landing at exterior doors other than the exit door required by rule 4781-6-03.9 of the Administrative Code shall not be required to comply with this requirement, but shall have a rise no greater than that permitted by this rule.
(b) Where a stairway of two or fewer risers is located on the exterior side of a door, other than the required exit door, a landing is not required for the exterior side of the door. The landing at the exterior side of the doorway shall not be more than eight and one-fourth inches (210 mm) below the top of the threshold.
(2) The width of each landing shall not be less than the door served. Every landing shall have a minimum dimension of twenty-four inches (610 mm) measured in the direction of travel, but no less than the dimension of the door that swings over the landing.
(3) Type of lock or latch. All egress doors shall be readily openable from the side from which egress is to be made without the use of a key or special knowledge or effort.
(L) Stairways.
(1) Width. Stairways shall not be less than thirty-six inches (914 mm) in clear width at all points above the permitted handrails height and below the required headroom height. Handrails shall not project more than four and one-half inches (114 mm) on either side of the stairway. Where a handrail is installed on one side, the minimum clear width of the stairway at and below the handrail height, including treads and landings, shall not be less than thirty-one and one-half inches (787 mm). Where handrails are provided on both sides, the minimum clear width of the stairway at and below the handrail height, including treads and landings, shall not be less than twenty-seven inches (698 mm).
(2) All stairs shall be illuminated in accordance with the requirements in the 2008 national electric code (NEC).
(M) Headroom. The minimum headroom in all parts of the stairway shall not be less than six feet eight inches (2036 mm) measured vertically from the sloped plane adjoining the tread nosing or from the floor surface of the landing or platform.
(N) Stair treads and risers.
(1) Riser height. The maximum riser height shall be eight and one-fourth inches (210 mm). The riser shall be measured vertically between leading edges of the adjacent treads. The greatest riser height within any flight of stairs shall not exceed the smallest by more than three-eighths of an inch (9.5 mm).
(2) Tread depth. The minimum tread depth shall be nine inches (229 mm). The tread depth shall be measured horizontally between the vertical planes of the foremost projection of adjacent treads and at a right angle to the tread's leading edge. The greatest tread depth within any flight of stairs shall not exceed the smallest by more than three-eighths of an inch (9.5 mm). Winder treads shall have a minimum tread depth of nine inches (229 mm) measured as above at a point twelve inches (305 mm) from the side where the tread is narrower. Winder treads shall have a minimum tread depth of six inches (152 mm) at any point. Within any flight of stairs, the greatest winder tread depth at the twelve-inch (305 mm) walk line shall not exceed the smallest by more than three-eighths of an inch (9.5 mm).
(3) Profile. The radius of curvature at the leading edge of the tread shall be no greater than nine-sixteenths of an inch (14.3 mm). A nosing not less than three-fourths of an inch (19 mm) but not more than one and one-fourth inches (32 mm) shall be provided on stairways with solid risers. The greatest nosing projection shall not exceed the smallest nosing projection by more than three-eighths of an inch (9.5 mm) between two stories, including the nosing at the level of floors and landings. Beveling of nosing shall not exceed one-half inch (12.7 mm). Risers shall be vertical or sloped from the underside of the leading edge of the tread above at an angle not more than thirty (0.51 rad) degrees from the vertical. Open risers are permitted, provided that the opening between treads does not permit the passage of a four-inch diameter (102 mm) sphere. Exceptions:
(a) A nosing is not required where the tread depth is a minimum of eleven inches (279 mm).
(b) The opening between adjacent treads is not limited on stairs with a total rise of thirty inches (762 mm) or less.
(O) Landings for stairways.
(1) There shall be a floor or landing at the top and bottom of each stairway unless a floor or landing is not required at the top of an interior flight of stairs, provided a door does not swing over the stairs.
(2) A flight of stairs shall not have a vertical rise greater than twelve feet (3658 mm) between floor levels or landings.
(3) The width of each landing shall not be less than the stairway served. Every landing shall have a minimum dimension of thirty-six inches (914 mm) measured in the direction of travel.
(P) Guards (railings) required. Porches, balconies, or raised floor surfaces located more than thirty inches (762 mm) above the floor or grade below shall have guards thirty-six inches (914 mm) in height. Open sides of stairs with a total rise of more than thirty inches (762 mm) above the floor or grade below shall have guards not less than thirty-four inches (864 mm) in height measured vertically from the nosing of the treads.
(1) Guard opening limitations. Required guards on open sides of stairways, raised floor areas, balconies, and porches shall have intermediate rails or ornamental closures that do not allow the passage of a sphere four inches (102 mm) or more in diameter.
(2) Side approach. Platform must be thirty-six inches in projection. Railing must be on one side and at the end of door swing.
(3) Exception. The triangular openings formed by the riser, tread, and bottom rail of a guard at the open side of the stairway are permitted to be of such size that a sphere six inches (152 mm) or more in diameter cannot pass through.