Rule 4123:1-21-02 | Personal protective clothing and equipment for structural fire fighting.
(A) The employer shall provide and require the use of personal protective clothing and equipment, as specified in this rule, when employees are required to work in a hazardous environment that may be encountered during structural fire fighting activities and under similar conditions during training activities.
(B) The employer shall assure that protective clothing protects the head, body, and extremities and consists of at least the following components: foot protection; hand protection; body protection; eye, face, and head protection; and respiratory protection.
(C) Personal protective clothing and equipment shall be properly sized for the wearer.
(D) Personal protective clothing and equipment that is damaged or otherwise defective to the point of voiding its intended protection shall be removed from service.
(E) Employers shall develop and require use of a written plan covering the safe use, limitations, care, inspection, maintenance, and replacement of the clothing and equipment required by this rule, and all affected employees shall be trained in accordance with such plan.
(F) Employers shall develop and retain records for the life of the protective clothing and equipment.
(G) Employer shall provide for the cleaning of personal protective clothing.
(H) Where employees choose to provide their own protective clothing and equipment, such clothing and equipment shall give equal or greater protection than that provided by the employer.
(I) It shall be the responsibility of the employee to properly use the equipment provided by the employer, as required in this rule.
(J) Body protection.
(1) Body protection shall consist of a protective coat and trousers, or equivalent protection.
(2) Protective clothing shall be flame-resistant, durable, light-weight, water-resistant, nonirritating to the skin, and cleanable as set forth in paragraph (J) of this rule.
(3) Protective clothing shall be cleaned per the manufacturer's recommendations.
(4) Protective clothing for structural fire fighting shall be repaired in accordance with manufacturer's requirements.
If protective clothing cannot be repaired properly without decreasing the protective qualities, it shall be replaced.
(5) Protective clothing shall be designed to give minimum interference to physical movement, the use of fire-fighting tools, and protective breathing apparatus.
(6) There shall be at least a two inch overlap of all layers of the protective coat and the protective trousers so there is no gaping of the total thermal protection when the protective garments are worn. The minimum overlap shall be determined by measuring the garments on the wearer, without SCBA, in both of the following positions:
(a) "Position A": standing, hands together, reaching overhead, as high as possible.
(b) "Position B": standing, hands together, reaching overhead, with body bent forward, to the side, and to the back, as much as possible.
(7) Employers that provide protective coats with protective resilient wristlets secured through a thumb opening shall be permitted to provide gloves of the gauntlet type for use with these protective coats. Employers that do not provide such wristlets attached to the protective coats shall provide gloves of the wristlet type for use with these protective coats.
(8) Design requirements.
(a) Protective clothing shall consist of an outer shell, moisture barrier, and thermal barrier.
(b) A means shall be provided to secure the moisture barrier and thermal barrier to the outer shell.
(c) Garments, including the front closure, shall be constructed in a manner that provides secure and complete moisture and thermal protection. Closure systems shall be secured with positive locking fasteners including, but not limited to, hooks and dees or zippers. Nonpositive fasteners, such as snaps or hook and pile tape, shall not be used as positive locking fasteners but shall be permitted to be utilized as supplementary garment closure devices.
(d) Moisture barriers and thermal barriers shall extend to within three inches (seventy-five mm) of the outer shell at the cuffs and hems of protective garments. At the neck, the coat moisture barrier and thermal barrier shall extend to the neckline seam. At the waist, the trouser moisture barrier and thermal barrier shall extend to the waistline seam. In coats, the moisture barriers and thermal barriers shall also extend to within one inch (twenty-five mm) of the sleeve end of the outer shell, and in trousers shall extend to within three inches (seventy-five mm) of the bottom outer shell hems. The liner system shall be attached at or adjacent to the end of the coat sleeves or the end of the trouser legs. Any mechanism used to attach the liner system at or adjacent to the end of the coat sleeves and the end of the trouser legs shall not be greater than one inch (twenty-five mm) between the attachment points, and shall not be expandable. Moisture barriers and thermal barriers shall be configured in a manner that provides continuous moisture and thermal protection.
(e) Cargo pockets, where provided, shall have a means of drainage of water and shall have flaps with a means of fastening them in the closed position.
(f) Trim used to meet visibility requirements shall be no less than two inches (fifty mm) wide and shall have retroreflective and fluorescent areas. Retroreflective areas of trim shall be no less than five-eighths inch (sixteen mm) wide. Fluorescent areas of trim shall have a minimum surface of two inches2/linear inch (fifty mm2/linear mm). Fluorescent and retroreflective areas of trim shall appear to be continuous at a distance of one hundred feet (30.5 m) for the length of the trim, with gaps between areas of retroreflectivity of no more than one-eighth inch (3mm).
(g) Trim affixed to protective garments for the purpose of meeting visibility requirements specified in paragraph (J)(12)(q) of this rule may be obscured by garment components such as, but not limited to, pockets, storm flaps, and reinforcing patches, as long as the minimum trim required in paragraphs (J)(8)(f), (J)(9)(e), and (J)(10)(c) of this rule is not obscured.
(h) The outer shell and each separable layer of protective garments shall have a label permanently and conspicuously attached to the inside upon which at least the following warnings and information are is printed:
(i) "This structural fire fighting garment meets the garment requirements of NFPA 1971, 2013 Edition."
(ii) Manufacturer's name, identification, or designation.
(iii) Manufacturer's address.
(iv) Country of manufacture.
(v) Manufacturer's element identification number, lot number, or serial number.
(vi) Date of manufacture (not coded).
(vii) Model name, number, or design.
(viii) Size.
(ix) Principal material(s) of construction.
(x) Cleaning precautions.
(xi) Certification organization's label, symbol, or identifying mark.
(i) The manufacturer shall provide a user information guide that describes the care, use, inspection, maintenance, limitations, and replacement of personal protective clothing.
(9) Additional requirements for protective coats.
(a) Protective coats shall provide protection to the upper torso, neck, arms, and wrists, excluding the hands and head.
(b) Protective coat hardware shall not penetrate through the outer shell, moisture barrier, and thermal barrier to contact the wearer's body when the coat is worn with closures fastened, unless the hardware is completely covered by external closure flaps.
(c) Each protective coat sleeve shall have a permanent protective wristlet, made of an inherently flame-resistant fiber, meeting requirements as specified in paragraph (J)(12) of this rule. The wristlet shall be attached to the protective coat sleeve in a manner that will not permit a gap in the thermal protection.
(d) Protective coats shall have a composite collar no less than three inches (seventy-five mm) in height at any point with a closure system. The collar and closure system shall consist of an outer shell, moisture barrier, and thermal barrier that meet all performance requirements as specified in paragraph (J)(12) of this rule.
(e) Each protective coat shall have a drag rescue device (DRD) installed in the upper torso portion of the coat. It shall be accessible from the exterior of the garment. It shall be designed so that when deployed, the DRD secures the fire fighter by the upper torso or shoulders so that the DRD pulls directly on the body and shall not pull only the garment.
(f) The trim configuration for the coat shall be in accordance with figure 1. The minimum trim pattern for the coat shall have one circumferential band of trim or a staggered three hundred sixty-degree visibility pattern meeting or exceeding the surface area of a continuous circumferential band around the bottom of the coat. Where a staggered pattern is used in the lower circumferential trim band, the lower edge of the upper trim piece shall not be higher than the upper edge of the lower trim piece. The lower edge of the circumferential band on the lower part of the coat shall be within one inch (twenty-five mm) of the coat hem's highest point. The front of the coat shall also have at least one band of horizontal trim at the chest level. No vertical stripes of trim shall be permitted on the front of the coat. The back of the coat shall also have a minimum of either two vertical stripes of trim, perpendicular to the bottom band and with one strip located on both the left and right sides of the of the back of the coat, or a minimum of one horizontal band of trim at the chest/shoulder blade level. The minimum trim configuration for each sleeve shall be one circumferential band, or a staggered three hundred sixty-degree visibility pattern meeting or exceeding the surface area of a continuous circumferential band, between the wrist and elbow level. Where trim on the coat intersects a zipper, a maximum gap in the trim of one inch (twenty-five mm) shall be permitted.
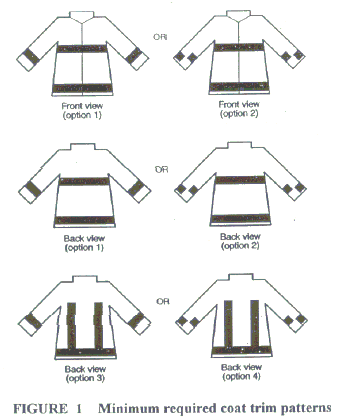
(10) Additional requirements for protective trousers.
(a) Protective trousers shall provide protection to the lower torso and legs, excluding the ankles and feet.
(b) Protective trouser hardware shall not penetrate through the outer shell, moisture barrier, and thermal barrier to contact the wearer's body when the trouser is worn with closures fastened, unless the hardware is located on or above the waistline or the hardware is completely covered by external closure flaps.
(c) The trim configuration for the trousers shall be in accordance with figure 2. Protective trouser trim shall include a circumferential band around each leg between the hem and knee. Where trim on the trousers intersects a zipper, a maximum gap in the trim of one inch (twenty-five mm) shall be permitted.
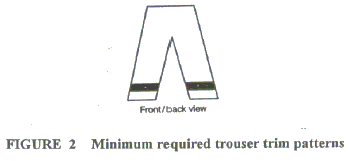
(11) Additional requirements for protective coveralls.
(a) That portion of the protective coverall which corresponds to the protective coat shall meet all requirements of paragraph (J)(9) of this rule.
(b) That portion of the protective coverall which corresponds to the protective trouser shall meet all requirements of paragraph (J)(10) of this rule.
(12) Performance requirements.
Protective garments shall be capable of withstanding all tests specified in NFPA 1971, "Protective Ensemble for Structural Fire Fighting, 2013 Edition."
(K) Foot protection.
(1) Design requirements.
(a) Protective footwear shall consist of a sole with heel, upper with lining, an insole, a puncture-resistant device, a ladder shank or whole sole equivalent and an impact and compression-resistant toecap permanently attached.
(b) Protective footwear shall be no less than ten inches in height when measured from the plane of the wear surface at the heel to the lowest point of the throat.
(c) The heel breast shall be no less than one-half inch or more than one inch. The heel breasting angle shall be no less than ninety degrees or more than one hundred thirty-five degrees. The edges shall not be less than, or extend more than, one-half inch laterally from the upper at any point. The width of the footwear heel shall be equal to or greater than the width of the sole at the intersection of the heel breast and the sole bottom.
(d) Metal parts shall not penetrate from the outside to the lining or insole at any point. All hardware and external fittings shall be free of rough spots, burrs, or sharp edges.
(e) No metal parts, including but not limited to nails or screws, shall be present or used in the construction or attachment of the sole (with heel) to the puncture-resistant plate, insole, or upper.
(f) The puncture-resistant device shall cover the maximum area of the insole.
(2) Performance requirements.
Protective footwear shall be capable of withstanding all tests specified in NFPA 1971, "Protective Ensemble for Structural Fire Fighting, 2013 Edition."
(3) Labeling requirements.
(a) Labels shall be legible to the naked eye and permanently affixed to all protective footwear by stamping, embossing, gluing, or stitching.
(b) Labels shall state:
(i) "This structural fire fighting protective footwear meets the footwear requirements of NFPA 1971, 2013 Edition. Do Not Remove This Label."
(ii) Manufacturer's name, identification, or designation.
(iii) Manufacturer's address.
(iv) Country of manufacture.
(v) Size or size range.
(vi) Model or stock number.
(vii) Manufacturer's element identification number, lot or serial number.
(viii) Month and year of manufacture.
(ix) Principle material(s) of construction.
(x) Cleaning precautions.
(xi) Certification organization's label, symbol, or identifying mark.
(L) Head protection.
(1) Head protection shall consist of a fire fighters' helmet and a protective hood. The helmet shall consist of a shell, an energy-absorbing system, a retention system, retroreflective and fluorescent markings, ear covers, and either a faceshield, or goggles, or both.
(2) Each helmet shall be durably and legibly labeled in a manner such that the label can be easily read without removing any permanent helmet part. Each label shall include the following information:
(a) "This structural fire fighting protective helmet meets the helmet requirements of NFPA 1971, 2013 Edition. Do not remove this label."
(b) Name, identification, or designation of manufacturer.
(c) Manufacturer's address.
(d) Country of manufacture.
(e) Manufacturer's element identification number, lot number, or serial number.
(f) Model number, name, or design.
(g) Month and year of manufacture (not coded).
(h) Cleaning precautions.
(i) Helmet size or size range.
(j) Principle material(s) of construction.
(k) Certification organization's label, symbol, or identifying mark.
(3) The helmet manufacturer shall place a unique manufacturer's part number, the symbol of the certification organization, and the words "NFPA 1971, 2013 Edition" permanently on each replaceable critical part of the goggle lens or faceshield.
(4) The helmet with faceshield/goggle component(s) stowed shall provide peripheral vision clearance of at least ninety-four degrees to each side when measured from the center of the eye with the helmet positioned according to its helmet positioning index on the Alderson fiftieth-percentile male headform.
(5) Where the goggle component is selected, the goggles shall be permitted to be unattached, not assembled, to the helmet
(6) When the faceshield or faceshield/goggle component is deployed in accordance with its helmet eye/face-positioning indexes on the Alderson fiftieth-percentile male headform, the faceshield or faceshield/goggle component shall provide at least the following field of vision when measured from the center of the eye:
(a) A dihedral angle of at least eighty-five degrees.
(b) An upper dihedral angle of at least ten degrees.
(c) A lower dihedral angle of at least forty degrees.
(7) There shall be no openings penetrating the shell except those provided by the manufacturer for mounting energy-absorbing systems, retention systems, and accessories.
(8) The addition of helmet accessories shall not interfere with the function of the helmet or its component parts and shall not degrade the helmet's performance below the requirements of this rule.
(9) The retention system shall include a chin strap and a nape device. The chin strap shall have a minimum width of three-fourths inch (nineteen mm).
(10) The helmet ear covers or portion of the helmet providing the coverage of the ears, when deployed with the helmet positioned on the ISO J headform according to its helmet positioning index, shall provide at least the following coverage from the reference plane downward to the lower edge of the ear covers:
(a) Three and three-fourths inches (ninety-five mm) where measured two inches (fifty mm) forward of the coronal plane.
(b) Four and three-fourths inches (one hundred twenty mm) where measured one inch (twenty-five mm) forward of the coronal plane.
(c) Five and one-eighth inches (one hundred thirty mm) where measured at the coronal plane.
(d) Five and one-eighth inches where measured at the midsagittal plane at the rear of the headform.
(11) All sewing thread used in the construction of helmets shall be made of inherently flame-resistant thread.
(12) Performance requirements.
Helmets shall be capable of withstanding all tests specified in NFPA 1971, "Protective Ensemble for Structural Fire Fighting, 2013 Edition."
Label durability and legibility.
Labels shall remain in place and shall be legible.
(M) Primary eye protection.
(1) Primary eye protection appropriate for a given specific hazard shall be provided for and used by employees exposed to that specific hazard.
(2) Primary eye protection shall meet the requirements of ANSI Z87.1, 2010 edition, practice for occupational and educational eye and face protection.
(3) The helmet faceshield, or flip-down eye shields, alone shall not be considered and shall not be used as primary eye protection.
(4) The full facepiece of SCBA, with the regulator attached, shall constitute face and primary eye protection.
(N) Protective hood
(1) The hood shall be designed to cover and provide the limited protection to the head, face, and neck areas that do not receive primary protection from the helmet or the "SCBA" facepiece.
(2) The hood shall be donned properly, in accordance with the manufacturer's instructions for wearing.
(3) The hood shall provide a minimum coverage (as measured on the ISO size J headform) as follows:
(a) On each side measured downward from the reference plane at the coronal plane of nine inches (two hundred thirty mm).
(b) In the back measured downward from the reference plane at the rear midsagittal plane of thirteen inches (three hundred thirty mm).
(c) In the front measured downward from the reference plane at the front midsagittal plane, excluding the face opening, of twelve inches (three hundred mm).
(4) The hood shall be designed with a face opening. Other than where the hood face opening is designed to interface with a specific "SCBA" facepiece or where the hood face opening is designed to be adjustable, the opening shall measure five and five-eighths inches, plus zero/minus one inch (one hundred forty-five mm, plus zero/minus twenty-five mm) in any direction when the hood is laid out in a relaxed condition on a flat surface, smoothed out, and with the face opening up.
(5) Where the hood face opening is provided with manual adjustment, the hood face opening shall be adjustable to achieve a face opening of five and five-eighths inches (one hundred forty-five mm).
(6) Where the hood face opening is designed to interface with a specific "SCBA" facepiece, the hood face opening shall overlap the outer edge of the specific "SCBA" facepiece-to-face seal perimeter by not less than one-half inch (thirteen mm).
(7) The hood shall have a label(s) permanently and conspicuously attached upon which the following information is legibly printed:
(a) "This structural fire fighting hood meets the hood requirements of NFPA 1971, 2013 Edition. Do Not Remove this label."
(b) Manufacturer's name, identification, or designation.
(c) Manufacturer's address.
(d) Country of manufacture.
(e) Manufacturer's element identification number, lot number, or serial number.
(f) Month and year of manufacture (not coded).
(g) Model name, number or design.
(h) Size or size range.
(i) Principle material(s) of construction.
(j) Cleaning precautions.
(k) Certification organization's label, symbol, or identifying mark.
(8) Where the hood is designed to be used with a specific "SCBA" facepiece(s), the hood manufacturer shall add to the hood product label the following statement: "This hood is designed to be used only with (Manufacturer to insert specific SCBA facepiece(s), model(s), and size(s) in this space) for compliance with NFPA 1971. This hood can only be used with the above noted facepiece(s)."
(9) Hoods shall be capable of withstanding all tests specified in NFPA 1971, "Protective Ensemble for Structural Fire Fighting, 2013 Edition."
Label durability and legibility.
Labels shall remain attached to the hood and shall be legible to the unaided eye.
(O) Personal alert safety system ("PASS").
(1) Each member shall be provided with, use, and activate his\her "PASS" device in all emergency situations that could jeopardize that person's safety due to atmospheres that could be IDLH, incidents that could result in entrapment, structural collapse of any type, or as directed by the incident commander or incident safety officer.
(2) Each "PASS" device shall be tested at least weekly and prior to each use.
(3) Each "PASS" device shall be maintained in accordance with the manufacturer's instructions.
(4) Each "PASS" device shall have a product label(s) permanently and conspicuously attached upon which the following information is legibly printed:
(a) "This PASS meets the requirements of NFPA 1982, Standard on Personal Alert Safety Systems (PASS), 2013 Edition. Do not remove this label."
(b) Manufacturer name, identification, or designation.
(c) Country of manufacture.
(d) Model name, number, or design.
(e) Identification, lot, or serial number.
(f) Month and year of manufacture (not coded).
(g) Recommended power source type and size if user replaceable.
(h) Certification organization's label, symbol, or identifying mark.
(i) "PASS" also shall meet the labeling requirements for "Class I, Division I Hazardous Locations of ANSI/UL 913, 2013 Edition, Standard for Intrinsically Safe Apparatus and Associated Apparatus for Use in Class I, II, and III, Division I Hazardous Locations."
(5) "PASS" devices can be designed to be either a stand-alone "PASS," or a "SCBA-integrated PASS," which can be removable/non-removable.
(6) PASS shall incorporate data logging in nonvolatile memory and, at a minimum, the following events shall be identified and recorded with the data log and shall also have a date and time stamp for each event in the data log:
(a) When the PASS is turned on;
(b) When the PASS activates any alarm or pre-alarm;
(c) When the PASS alarm is activated by the user;
(d) When the PASS alarm was reset;
(e) When the PASS was turned off;
(f) When the PASS low power source warning signal activates.
The data logging information shall be downloadable by the employer.
(7) "PASS" shall incorporate a mode selection device or devices to allow for operation in at least three modes: "Off," "Alarm," and "Sensing."
(a) All mode selection devices shall be capable of being switched to the alarm or sensing mode by a single gloved hand.
(b) Only one action shall be required to switch the mode selection device(s) from any mode to alarm.
(c) When "PASS" is sounding the alarm signal it shall require at least two separate and distinct manual actions to silence the alarm signal.
(8) PASS shall be provided with a light source capable of providing a visual indication of mode status as well as an audible source capable of providing an aural indication of a change in the mode selection when switching from "off" to "sensing," "off" to "alarm," and "alarm" to sensing."
(9) "PASS" shall incorporate a motion detector, and while in the sensing mode, shall sound the alarm signal when the "PASS" is motionless for thirty seconds, plus five/minus zero seconds. The alarm signal shall be preceded by a pre-alarm signal that shall sound ten seconds, plus three/minus zero seconds, before the sounding of the alarm signal.
(a) The motion detector shall be operable regardless of the angle of deployment of the "PASS."
(b) Any failure of the motion detector shall cause the "PASS" to sound the alarm signal within thirty seconds, plus five/minus zero seconds, of such failure.
(10) "PASS" shall emit an audible operational signal within one second of being switched to sensing mode, indicating to the user that the device is functioning properly.
(11) "PASS" shall have at least an audible primary pre-alarm signal. The primary pre-alarm signal shall be a distinct and different sound from the alarm signal. This signal shall sound no more than ten seconds prior to the sounding of the alarm signal.
(12) "PASS" shall sound the alarm signal when switched to the alarm mode. The alarm signal shall have a duration of at least one hour at a sound pressure level of not less than ninety-five dBa.
(13) While in the sensing mode, "PASS" shall emit a recurrent audible low power source warning signal when the battery voltage is depleted to the level that will maintain the alarm signal level of at least ninety-five dBa for at least one hour. This sound shall be distinct and different from the pre-alarm and alarm signals. The low power source warning signal shall have an interval of not greater than thirty seconds.
(14) The cancellation of the pre-alarm signal or the silencing of the alarm signal shall automatically reset the "PASS" to the sensing mode.
(15) "PASS" devices shall be capable of withstanding all performance requirement tests specified in NFPA 1982, "Personal Alert Safety Systems (PASS), 2013 Edition."
Product label durability.
Product labels shall remain attached to the "PASS" and shall be legible to the unaided eye.
(P) Respiratory protection.
(1) All fire fighters exposed to hazardous atmospheres from fires and other emergencies, or where the potential for such exposure exists, shall be provided with self-contained breathing apparatus ("SCBA") approved by the national institute for occupational safety and health (NIOSH) and the national fire protection association (NFPA).
(2) The fire department shall adopt and maintain a respiratory protection program that addresses the selection, inspection, safe use, and maintenance of respiratory protection equipment, training in its use, and the assurance of air quality testing.
(3) All members who might be required to use respiratory protection equipment shall be medically certified by a physician, or by a state of Ohio licensed health care professional who can perform medical evaluations under the supervision of a physician, on an annual basis. Medical certification can be obtained by a medical examination, or by using the medical questionnaire as referenced in CFR 1910.134 Appendix C.
(4) The facepiece seal capability of each member qualified to use "SCBA" shall be verified by quantitative fit testing on an annual basis and whenever new types of "SCBA" or facepieces are issued. Each new member shall be tested before being permitted to use SCBA in a hazardous atmosphere. Only members with a properly fitting facepiece shall be permitted by the fire department to function in a hazardous atmosphere with "SCBA."
(5) Only "SCBA" with an approved service life of thirty minutes or more shall be considered acceptable.
(6) The following "SCBAs" shall be considered to meet the requirements of this rule:
(a) Open circuit "SCBA" of the positive-pressure type that operate only in the pressure demand mode.
(b) Open circuit "SCBA" of the positive-pressure type, equipped with an air flow control device for doffing and donning purposes only. Such air flow control device shall not permit the continued use of the "SCBA" in the demand mode after donning.
(c) Closed circuit "SCBA" with a rated service life of more than two hours and a minimum protection factor of five thousand, as determined by an acceptable quantitative fit test performed on each individual. Such "SCBA" are acceptable only when long-duration respiratory protection is deemed necessary by the employer. Closed circuit "SCBA" shall operate in the positive-pressure mode only.
(7) Open circuit "SCBA" approved by NIOSH for use in the demand mode or for use in both the demand mode and the pressure demand mode are prohibited.
(8) Breathing air used to fill SCBA cylinders shall meet the requirements specified in NFPA 1989, "Standard on Breathing Air Quality for Emergency Services Respiratory Protection."
(9) Breathing air quality shall be tested quarterly by an accredited testing laboratory and shall meet the requirements of paragraph (P)(8) of this rule. This shall also apply to vendor-supplied and other fire department-supplied compressed breathing air. The department receiving supplied air shall require the supplier to provide documentation that the air received has been tested quarterly and that it meets the requirements of paragraph (P)(8) of this rule. Written records shall be maintained.
(10) The employer shall not permit any known interference with the facepiece-to-face seal or with the operation of the exhalation valve on the full facepiece of an "SCBA" on employees who are exposed to hazardous atmospheres from fires and other emergencies or where the potential for such exposure exists.
(11) Respiratory equipment shall be inspected, maintained, and repaired in accordance with the manufacturer's recommendations. Maintenance shall include at least:
(a) A written record of such inspection and maintenance for each piece of equipment.
(b) Regulator calibration performed by a manufacturer-authorized person at no more than twelve-month intervals.
(12) All compressed air cylinders used with self-contained breathing apparatus shall meet department of transportation (DOT) and NIOSH criteria.
(13) SCBA cylinders shall be hydrostatically tested within the periods specified by the manufacturer and by DOT and NIOSH.
(14) The practice of buddy breathing, also known as an emergency escape breathing support system (EEBSS), may be utilized where it is accomplished through the use of an NFPA and NIOSH-approved connection that does not compromise the system integrity of either of the users giving or receiving air.
(15) The use of a universal air connection for rapid refilling of SCBA while being worn by the user shall only be done under the following conditions:
(a) Manufacturer permitted, NIOSH-approved fill options are used.
(b) An imminent life threatening situation occurs that requires immediate action to prevent the loss of life or serious injury.
(c) Prior to a life threatening situation occuring that could require immediate action to prevent the loss of life or serious injury.
(d) The risk assesment process has identified procedures for limiting personnel exposure during the refill process and has provided for adequate equipment inspection and member safety.
(Q) Hand protection.
(1) Hand protection shall consist of properly sized protective gloves or a glove system which allows dexterity of hand movement and a sense of feel for objects.
(2) Gloves of the wristlet type or other interface component shall be required if the protective coat does not provide a protective resilient wristlet with a thumb opening.
Gloves of the gauntlet type shall be allowed if the protective coat provided has a protective resilient wristlet with a thumb opening.
(3) Gloves shall be maintained and repaired in accordance with the manufacturer's requirements. If gloves cannot be repaired properly without decreasing the protective qualities required by this rule, they shall be replaced with gloves that meet the requirements of paragraph (Q) of this rule.
(4) A label which includes the following information shall be permanently attached to each glove:
(a) "This structural fire fighting glove meets the glove requirements of NFPA 1971, Standard on Protective Ensemble for Structural Fire Fighting, 2013 Edition. Do Not Remove This Label."
(b) Manufacturer's name, identification, or designation.
(c) Manufacturer's address.
(d) Manufacturer's element, identification , lot or serial number.
(e) Month and year of manufacture (not coded).
(f) Size or size range.
(g) Principle material(s) of construction.
(h) Cleaning precautions.
(i) Certification organization's label, symbol, or identifying mark.
(5) Design requirements.
(a) Gloves for structural fire fighters shall be made of durable outer material designed to withstand the effects of flame, heat, vapor, liquids, sharp objects, and other hazards that are encountered during structural fire fighting.
(b) Gloves shall be designed to give minimum interference to physical movement, the use of fire fighting tools, and "SCBA."
(c) Wrist protection shall be designed to prevent burns or injury by providing complete covering under all conditions to the wrist area.
(d) Wrist protection may be provided by either of the following methods:
(i) Gloves, including wristlets, that extend no less than two inches above the wrist crease as shown in figure 4 to this rule; or
(ii) Wristlets attached to the sleeves of the protective coat that extend to fit around the palm of the hand (see figure 4).

(e) Gloves shall be close-fitting above the wrist to restrict entry of liquids, embers, and other foreign particles.
(f) The glove material in contact with the skin shall be nonirritating.
(6) Performance requirements.
Gloves shall be capable of withstanding all tests specified in NFPA 1971, "Protective Ensemble For Structural Fire Fighting, 2013 Edition."
Label durability and legibility.
Labels shall remain in place, and shall be legible.
(R) Fall protection.
(1) Life safety rope.
(a) Technical-use life safety rope shall have a diameter of three-eighths inch (9.5 mm) or greater and less than one-half inch(12.5 mm). It shall have a minimum breaking strength of not less than four thousand four hundred ninety-six lbf (twenty kn). The minimum elongation shall be less than one per cent at ten per cent of breaking strength, and the maximum elongation shall not be more than ten per cent at ten per cent of breaking strength.
(b) General-use life safety rope shall have a diameter seven-sixteenths inch ( eleven mm) or greater and not more than five-eighths inch ( sixteen mm). It shall have a minimum breaking strength of not less than eight thousand nine hundred ninety-two lbf (forty kn). The minimum elongation shall not be less than one per cent at ten per cent of breaking strength, and the maximum elongation shall not be more than ten per cent at ten per cent of breaking strength.
(c) Life safety rope shall be constructed of virgin fiber and shall be of block creel construction. Load-bearing elements shall be constructed of continuous filament fiber.
(d) Fiber used for life safety rope shall have a melting point of no less than four hundred degrees Fahrenheit.
(e) Each life safety rope shall have a product label. The label shall be permitted to be a hang tag affixed to each individual life safety rope or shall be permitted to be printed on a sheet that is inserted and sealed in the packaging that contains the life safety rope. At least the following information shall be legibly printed on the label:
(i) "This rope meets the life safety rope requirements of NFPA 1983, Standard on Life Safety Rope and Equipment for Emergency Services, 2012 Edition."
(a) Class: manufacturer to insert specific information regarding use rope.
(b) Minimum breaking strength: manufacturer to insert specific information regarding pound/(Kn).
(c) Diameter: manufacturer to insert specific information regarding inch/(mm).
(d) Type of fiber(s).
(ii) Manufacturer's name, identification, or designation.
(iii) Manufacturer's address.
(iv) Country of manufacturer.
(v) Manufacturer's product identification.
(vi) Manufacturer's model, style, serial, or lot number.
(vii) Certification organization's label, symbol, or identifying mark.
(viii) Elongation at three hundred lbf (1.35 kN), at six hundred lbf (2.7 kN), and at one thousand lbf (4.4 kN).
(f) In addition to the product label specified in paragraph (R)(5)(e) of this rule, each life safety rope shall be marked for its full length by insertion of a continuous identification tape. At least the following statement and information shall be legibly printed on the tape not less than once every thirty-nine inches (one meter):
(i) "Meets requirements for life safety rope of NFPA 1983."
(ii) Certification organization's label, symbol, or identifying mark.
(iii) Name of manufacturer.
(iv) Year and quarter of manufacturer (not coded).
(g) The manufacturer of life safety rope shall furnish the purchaser with at least use criteria, inspection procedures, maintenance procedures, and retirement criteria.
(h) Life safety rope shall be inspected after being used for rescue at fires or other emergency incidents or for training. It may be reused if inspected before and after each such use in accordance with the manufacturer's instructions and provided that:
(i) The rope has not been visually damaged by exposure to heat, direct flame impingement, chemical exposure, or abrasion; and
(ii) The rope has not been subjected to any impact load; and
(iii) The rope has not been exposed to chemical liquids, solids, gases, mists, or vapors of any material known to deteriorate rope; and
(iv) The rope passes inspection when inspected by a qualified person following the manufacturer's inspection procedures.
(2) Life safety harness.
(a) Life safety harnesses shall be designed and designated in accordance with one of the following classes:
(i) Harness that fastens around the waist and around thighs or under buttocks and designed for rescue with a design load of six hundred lbf shall be designated as class II life safety harness.
(ii) Harness that fastens around waist, around thighs or under buttocks, and over shoulders, designed for rescue with a design load of six hundred lbf shall be designated as class III life safety harness. Class III life safety harness shall be permitted to consist of one or more parts.
(b) Life safety harness shall be permitted to be adjustable within a range of sizes, provided in a range of sizes, or custom-fitted for individuals.
(c) Load-bearing textile materials used to construct life safety harness shall be constructed of virgin, synthetic, continuous filament fiber.
(d) All webbing ends shall be secured by heat-sealing or by another method that prevents unraveling.
(e) All thread shall be compatible with webbing used, shall meet the strength and heat resistance requirements specified in paragraph (R)(2)(k) of this rule, and shall allow for ease of inspection. All stitching breaks or ends shall be backtacked no less than one one-half inch (thirteen mm).
(f) Life safety harness shall have at least one load bearing attachment point located at the front waist or sternal location of the harness.
(g) Castings shall meet class I, grade A requirements of SAE-STD 2175A, "castings, classification and inspection of."
(h) Where a buckle is an integral part of a life safety harness, the buckle manufacturer shall provide written evidence that all load-bearing buckles have been proof-loaded to at least two thousand four hundred seventy-three lbf (eleven kN).
(i) Each life safety harness shall have permanently affixed a product label embossed, printed, sewn, stapled, riveted, or otherwise permanently attached with a metal label plate. At least the following compliance statement shall be on the product label:
(i) "This life safety harness meets the harness requirements of NFPA 1983, "Life Safety Rope and Equipment for Emergency Services, 2012 edition"; class: (manufacturer to insert specific information regarding class)."
The class designation shall be as determined by the certification organization.
(ii) Name, identification, or designation of manufacturer.
(iii) Manufacturer's address.
(iv) Country of manufacture.
(v) Manufacturer's product identification.
(vi) Manufacturer's lot, model, style, or serial number.
(vii) Certification organization's label, symbol, or identifying mark.
(j) In addition, for harnesses, at least the following information shall be provided on the label:
(i) For class II harnesses: "Fits waist size (manufacturer to insert specific size(s)."
(ii) For one-piece class III harnesses: "Fits waist size (manufacturer to insert specific size(s); fits height (manufacturer to insert specific height(s)."
(iii) For multiple-piece class III harnesses: "Fits waist size (manufacturer to insert specific size(s); fits height or chest size (manufacturer to insert specific height(s) or chest size(s); fits height (manufacturer to insert specific height(s). This is one part of a multiple-piece harness and must be used in conjunction with component part number (manufacturer to insert specific component part number[s]) in order to fully meet the criteria of class III harness.
(k) Life safety harness shall be capable of withstanding all tests specified in NFPA 1983, " Life Safety Rope and Equipment for Emergency Services, 2012 Edition," with the following results:
(i) Static test - upright (for class II and III).
(ii) Static test - horizontal (for class II and III).
(iii) Static test - head down (for class III).
Class II and III life safety harness shall not release from the test torso, the harness buckles and adjusting devices shall not slip more than one inch (twenty-five mm), and the harness shall show no visible signs of damage that would affect its function.
(iv) For class III life safety harness that includes shoulder attachment points, such shoulder attachment points shall be tested only during the static test - upright. The shoulder attachment points shall not release from the test torso, and shall show no signs of damage that would affect their function.
(v) Fiber and thread used in the construction of life safety harness shall have a melting point of no less than four hundred degrees Fahrenheit.
(vi) Where class II and III life safety harness include side "D-rings" and attachment points designated by the manufacturer as positioning attachments only, these attachments shall show no visible signs of damage that affect its function.
(vii) All metal hardware and parts shall show no more than light surface-type corrosion or oxidation, and remain functional.
(l) The manufacturer of life safety harness shall furnish the purchaser with at least use criteria, inspection procedures, maintenance procedures, and retirement criteria for the product.
(3) Belt system.
(a) Belts shall be designed and designated in accordance with one of the following types:
(i) A belt that fastens only around the waist and is intended for use as a positioning device for a person on a ladder shall be designated as a ladder belt.
(ii) A belt that fastens only around the waist and is intended for use as a positioning device for a person on a ladder and also intended for use only by the wearer as an emergency self-rescue device shall be designated as a ladder/escape belt.
(b) All belts shall be permitted to be adjustable within a range of sizes, provided in a range of sizes, or custom-fitted for individuals.
(c) Load-bearing textile materials used in the construction of all belts shall be made of virgin, synthetic, continuous filament fiber.
(d) All belts shall have webbing ends secured by heat sealing or by another method that prevents unraveling.
(e) All thread utilized in the construction of all belts shall be compatible with the webbing used and shall allow for ease of inspection. All stitching breaks or ends shall be backtacked not less than one-half (thirteen mm).
(f) The ladder belt tether or device that connects the wearer to a ladder shall be permanently affixed to the ladder belt and shall not be greater than twenty-four inches (six-hundred ten mm) in length. This requirement applies only to ladder belts as defined in paragraph (R)(3)(a)(i) of this rule.
(g) Each belt shall have permanently affixed a product label embossed, printed, sewn, stapled, riveted, or otherwise permanently attached with a metal plate. At least the following compliance statement shall be on the product label:
(i) "This belt meets the belt requirement of NFPA 1983, "Life Safety Rope and Equipment for Emergency Services, 2012 Edition"; type (manufacturer to insert specific type)."
The belt type designation shall be determined by the certification organization.
(ii) "Fits waist size (manufacturer to insert specific waist size(s)."
(iii) Name, identification, or designation of manufacturer.
(iv) Manufacturer's address.
(v) Country of manufacture.
(vi) Manufacturer's product identification.
(vii) Manufacturer's lot, model, style, or serial number.
(viii) Certification organization's label, symbol, or identifying mark.
(h) All ladder belts and ladder/escape belts shall be capable of withstanding all tests specified in NFPA 1983, " "Life Safety Rope and Equipment for Emergency Services, 2012 Edition."
(i) The manufacturer of belts shall furnish the purchaser with at least use criteria, inspection procedures, maintenance procedures, and retirement criteria for the product.
(4) Auxiliary equipment.
(a) Auxiliary equipment shall be designated by the manufacturer for its intended use and design load as either escape, light-use, or general-use.
(i) Escape shall apply to equipment intended for the sole use of the rescuer for personal escape or self-rescue.
(ii) Technical-use shall apply to equipment intended for a design load of three hundred lbf (1.33 kN).
(iii) General-use shall apply to equipment intended for design loads of six hundred lbf (2.67 kN).
(b) Load-bearing hardware shall be constructed of forged, machined, stamped, extruded, or cast metal. Castings shall meet Class I, Grade A requirements of SAE-STD 2175A, "Castings, Classification and Inspection of."
(c) Rope grab devices shall be designated for either technical use or for general use.
(d) All load-bearing buckles shall have been proof loaded to at least two thousand four hundred seventy-three lbf (eleven kn).
(e) Snap-link and carabiner gates shall be self-closing and of a locking design.
(f) Webbing used to construct auxiliary equipment software shall be constructed of virgin, synthetic, continuous filament fiber.
(g) All webbing ends shall be secured by heat sealing or by another method that prevents unraveling.
(h) All thread used to construct auxiliary equipment software shall be compatible with webbing used and shall allow ease of inspection. All stitching breaks or ends shall be backtacked not less than one-half inch (thirteen mm).
(i) Each item of auxiliary equipment shall be permitted to have a hang tag affixed to each individual auxiliary equipment item or shall be permitted to be printed on a sheet that is inserted and sealed in the packaging that contains the item. At least the following compliance statements shall be on the product label:
(i) "This (insert name of equipment item here) meets the auxiliary equipment requirements of NFPA 1983, Life Safety Rope and Equipment for Emergency Services, 2012 Edition."
(ii) Name, identification, or designation of manufacturer.
(iii) Manufacturer's address.
(iv) Country of manufacture.
(v) Manufacturer's product identification.
(vi) Manufacturer's lot, model, style, or serial number.
(vii) Certification organization's label, symbol, or identifying mark.
(viii) Auxiliary equipment shall also be stamped, engraved, or otherwise permanently marked with a "G" for general-use; "T" for technical-use; "E" for escape, as designated in paragraphs (R)(4)(a)(i) to (R)(4)(a)(iii) of this rule.
(ix) Portable anchor devices shall add to the product label: "Minimum breaking strength and rating are determined at the configuration of lowest strength per manufacturer's instructions."
(x) Rigging and anchor straps shall add to the product label: "Minimum breaking strength and rating are determined using a basket (U) configuration. In addition, this strap has a minimum breaking strength of: [enter number here] kN in a choker configuration; [enter number here] kN when pulled end to end."
(xi) Where detachable components must be used with the auxiliary equipment in order for the auxiliary equipment to be compliant, shall add to the product label: "To be compliant with NFPA 1983, the following additional components must be used in conjunction with this (insert type of auxiliary equipment here)."
(j) All auxiliary equipment shall be capable of withstanding all tests specified in NFPA 1983, " "Life Safety Rope and Equipment for Emergency Services, 2012 Edition."
(k) The manufacturer of auxiliary equipment shall furnish the purchaser with at least use criteria, inspection procedures, maintenance procedures, and retirement criteria for the product.
(5) Escape rope.
(a) Escape rope shall be constructed of virgin fiber and shall be of block creel construction. Load-bearing elements shall be constructed of continuous filament fiber.
(b) Escape rope shall have a diameter of 0.295 inch (19/64th inch) (7.5 mm) or greater and less than three-eighths inch (9.5 mm).
(c) Escape rope shall have a minimum breaking strength of not less than three thousand thirty-four lbf (13.5 kN).
(d) Elongation of all new escape rope shall be less than one per cent and not more than ten per cent at ten per cent of breaking strength.
(e) Fiber utilized for all escape rope shall not have a melting point of less than four hundred degrees Fahrenheit (two hundred four degrees Celsius).
(f) Each escape rope shall have a product label. The product label shall be permitted to be a hang tag affixed to each individual escape rope or shall be permitted to be printed on a sheet that is inserted and sealed in the packaging that contains the rope. At least the following information shall be legibly printed on the label:
(i) "This rope meets the escape rope requirements of NFPA 1983, Life Safety Rope and Equipment for Emergency Services, 2012 Edition."
(a) Minimum breaking strength: (manufacturer will insert specific information regarding lbf/(kn).
(b) Diameter: (manufacturer will insert specific information regarding inch/(mm).
(c) Type of fiber(s).
(ii) Manufacturer's name, identification, or designation.
(iii) Manufacturer's address.
(iv) Country of manufacture.
(v) Manufacturer's product identification.
(vi) Manufacturer's product identification.
(vii) Certification organization's label, symbol, or identifying mark.
(viii) Elongation at three hundred lb (1.35 kN), at six hundred lb (2.7 kN), and at one thousand lb (4.4 kN).
(g) In addition to the product label specified in paragraph (R)(5)(f) of this rule, each escape rope shall be marked for its full length by insertion of a continuous identification tape. At least the following statement and information shall be legibly printed on the tape not less than once every thirty-nine inches (one meter):
(i) "Meets requirements for escape rope of NFPA 1983."
(ii) Certification organization's label, symbol, or identifying mark.
(iii) Name of manufacturer.
(iv) Year and quarter of manufacturer (not coded).
(h) The manufacturer of escape rope shall furnish the purchaser with at least use criteria, inspection procedures, maintenance procedures, and retirement criteria.
(6) Throwline.
(a) Throwline shall be constructed of virgin fiber and shall be of block creel construction. Load-bearing elements shall be constructed of continuous filament fiber.
(b) Throwline shall have a diameter of 19/64th inch (seven mm) or greater, but less than 3/8th inch (9.5 mm).
(c) The minimum breaking strength for new throwline shall not be less than two thousand nine hundred twenty-three lbf (thirteen kn).
(d) New throwline shall be tested for the ability to float and shall float.
(e) Each throwline shall have a product label. The throwline product label shall be permitted to be a hang tag affixed to each individual throwline or shall be permitted to be printed on a sheet that is inserted and sealed in the packaging that contains the throwline. At least the following information shall be legibly printed on the label:
(i) "This rope meets the throwline requirements of NFPA 1983, Life Safety Rope and Equipment for Emergency Services, 2012 Edition."
(a) Minimum breaking strength: (manufacturer to insert specific information regarding lbf/(kn).
(b) Diameter: (manufacturer to insert specific information regarding inch/(mm).
(c) Type of fiber(s),
(ii) Manufacturer's name, identification, or designation.
(iii) Manufacturer's address.
(iv) Country of manufacture.
(v) Manufacturer's product identification.
(vi) Manufacturer's model, style, serial, or lot number.
(vii) Certification organization's label, symbol, or identifying mark.
(f) In addition to the product label specified in paragraph (R)(6)(e) of this rule, each throwline shall be marked for its full length by insertion of a continuous identification tape. At least the following statement and information shall be legibly printed on the tape not less than once every thirty-nine inches (one meter):
(i) "Meets requirements for throwline of NFPA 1983."
(ii) Certification organization's label, symbol, or identifying mark;
(iii) Name of manufacturer;
(iv) Year and quarter of manufacture.
Last updated June 11, 2021 at 10:39 AM